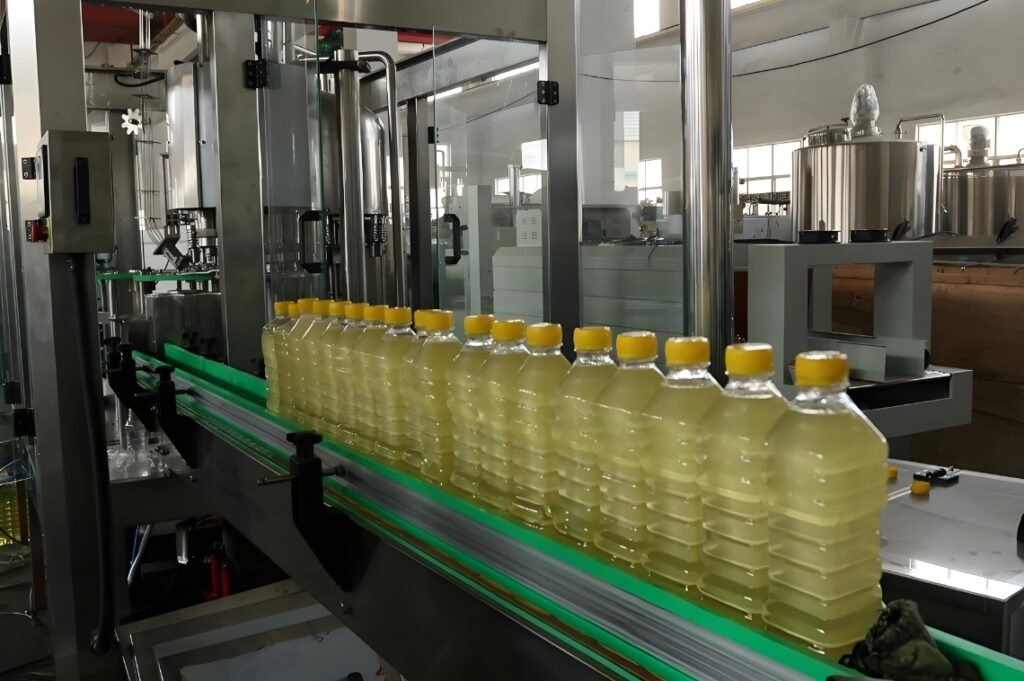
Liquid filling machines are critical for many industries. They help pack products efficiently, reducing labor and time. But, like any machine, they can sometimes face issues. Knowing how to troubleshoot these problems can help keep your production line running smoothly.
In this article, we will explore some common problems with filling machines and provide tips on how to solve them. By understanding these issues and their solutions, you can avoid downtime and maintain product quality.
1. Inconsistent Filling Volumes
One of the most common issues with a filling machine is inconsistent filling levels. This problem can lead to underfilling or overfilling, causing product waste and customer dissatisfaction.
Causes:
- Incorrect machine calibration
- Worn-out or damaged nozzles
- Inconsistent liquid pressure
- Air trapped in the filling system
Solutions:
- Check the calibration. Ensure the automatic filling machine is set to the correct volume. Recalibrate if necessary.
- Inspect the nozzles. Replace any damaged or worn-out nozzles.
- Monitor the liquid pressure. Ensure consistent pressure is maintained throughout the filling process.
- Remove trapped air. Air bubbles can cause inconsistent filling. Use an air purging process to eliminate air from the system.
2. Machine Not Dispensing Properly
Sometimes the filling machine may not dispense the liquid as it should. This can stop production or lead to incomplete fills.
Causes:
- Clogged nozzles
- Blocked or dirty hoses
- Faulty valves
Solutions:
- Clean the nozzles regularly to prevent clogs. Use the proper cleaning method based on the product being filled.
- Inspect and clean the hoses. Blocked hoses can prevent liquid flow, so keeping them clear is essential.
- Check the valves. Faulty valves can affect the machine’s ability to dispense liquid properly. Replace them if necessary.
3. Foaming During Filling
Foaming is a frequent issue, especially with certain liquids like soaps, shampoos, or carbonated beverages. It can lead to spillage and uneven fills.
Causes:
- Filling speed too high
- Incorrect nozzle positioning
- High product viscosity
Solutions:
- Reduce the filling speed. Slowing down the process can minimize foam.
- Adjust the nozzle position. Make sure the nozzle is close to the container’s bottom to reduce air mixing with the liquid.
- Check the liquid’s viscosity. Thicker liquids tend to foam more. Adjust the automatic filling machine settings accordingly.
4. Leaks from the Machine
Leaks can occur around the machine or at the nozzles, leading to product waste and possible machine damage.
Causes:
- Loose fittings
- Worn-out seals or gaskets
- Overfilled containers
Solutions:
- Tighten all fittings regularly to prevent leaks.
- Inspect and replace any worn-out seals or gaskets to stop leakage.
- Make sure containers are not overfilled, as this can lead to spills.
5. Slow Production Speed
Sometimes, the automatic filling machine may operate slower than expected. This reduces efficiency and can delay production schedules.
Causes:
- Incorrect machine settings
- Blockages in the system
- Worn-out machine components
Solutions:
- Adjust the machine settings for optimal speed. Check the manufacturer’s instructions for recommended settings.
- Check for blockages. Ensure there is no obstruction in the nozzles, hoses, or valves.
- Replace any worn-out parts to restore the machine’s speed.
6. Air Bubbles in the Filled Product
Air bubbles in the product can reduce the quality of the final product and lead to customer complaints.
Causes:
- Air trapped in the liquid supply
- Filling speed too fast
- Incorrect nozzle placement
Solutions:
- Purge the air from the liquid supply before starting the filling process.
- Slow down the filling speed to allow the liquid to settle properly in the container.
- Position the nozzle correctly, ensuring it reaches the bottom of the container for smooth filling.
7. Machine Jams During Operation
Jams are another common issue in filling machines. This can bring production to a halt, causing delays.
Causes:
- Debris or foreign objects in the system
- Blockages in the filling pathway
- Mechanical malfunctions
Solutions:
- Regularly clean the machine to remove any debris or contaminants.
- Check the filling pathway for blockages. Clear any obstructions before restarting the machine.
- Inspect the machine for mechanical issues and replace any malfunctioning parts.
8. Dripping Nozzles
Dripping nozzles can cause product waste and make a mess around the machine.
Causes:
- Worn-out nozzle seals
- Incorrect nozzle shut-off timing
- Residue build-up in the nozzle
Solutions:
- Replace the seals on the nozzles regularly to prevent drips.
- Adjust the shut-off timing to stop the flow immediately after the filling is complete.
- Clean the nozzles to remove any residue that could cause dripping.
9. Filling Accuracy Problems
For businesses that rely on precise filling, accuracy issues can lead to losses or regulatory problems.
Causes:
- Incorrect calibration
- Variations in product viscosity
- Uneven liquid pressure
Solutions:
- Recalibrate the machine to ensure the correct fill levels.
- Monitor product viscosity and adjust the machine settings accordingly.
- Ensure the automatic filling machine maintains consistent pressure during the filling process.
10. Electrical Issues
Sometimes the filling machine may face electrical problems, such as failure to power up or sudden shutdowns.
Causes:
- Faulty wiring
- Damaged power supply
- Overloaded circuits
Solutions:
- Inspect the wiring and repair any damaged connections.
- Replace the power supply if it is not working correctly.
- Avoid overloading circuits by ensuring the machine is connected to an appropriate power source.
Preventive Maintenance Tips for Filling Machines
Preventive maintenance can help avoid many of the issues mentioned above. Here are some tips to keep your filling machine running smoothly:
1. Regular Cleaning
Clean the machine daily or after every production run to prevent residue build-up. This helps reduce clogs, leaks, and other issues.
2. Routine Inspections
Inspect the machine regularly for any signs of wear and tear. Check seals, gaskets, and nozzles frequently to avoid breakdowns.
3. Lubricate Moving Parts
Keep the moving parts of your automatic filling machine lubricated. This reduces friction and prevents the machine from slowing down or jamming.
4. Calibrate Often
Regular calibration is essential for maintaining filling accuracy. Calibrate the machine whenever you notice inconsistent fills.
5. Replace Worn-Out Parts
Don’t wait for parts to break. Replace worn-out parts as part of your routine maintenance to prevent unexpected shutdowns.
Proper troubleshooting of your filling machine can save time and money. By identifying and solving common issues like inconsistent filling volumes, leaks, or clogs, you can maintain efficiency and prevent production delays.
Regular maintenance, including cleaning and inspections, will also keep your automatic filling machine running smoothly. Understanding how to troubleshoot and care for your machine will help you get the most out of your equipment while ensuring high-quality production.