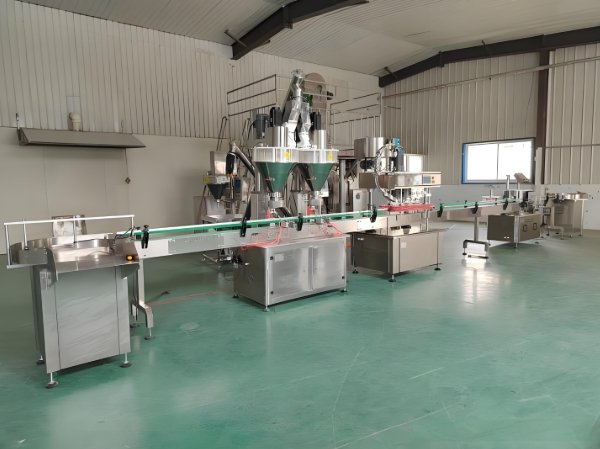
Filling powdered products manually is time-consuming and prone to errors. A Powder Filling Machine offers a more efficient, precise, and scalable solution. Whether for small-scale production or industrial operations, these machines outperform manual methods in every way.
This article explains why switching to a Powder Filling Machine, especially an Automatic Filling Machine, is a smart choice for businesses seeking to optimize their operations.
Challenges of Manual Filling
1. Inconsistent Accuracy
Manual filling often results in overfilling or underfilling.
- Accuracy depends on the skill of the operator.
- Variability leads to inconsistent product weight.
2. Slow Production Speeds
Filling powders manually is time-intensive.
- Low output limits production capacity.
- Difficult to meet high demand efficiently.
3. Increased Labor Costs
Manual filling requires more workers.
- Labor-intensive processes are expensive.
- Human errors increase wastage and rework.
4. Hygiene Concerns
Manual handling increases contamination risks.
- Lack of sterile processes affects product quality.
- Compliance with hygiene standards becomes challenging.
Benefits of Using Powder Filling Machines
Switching to a Powder Filling Machine solves these challenges.
1. Enhanced Accuracy
Machines deliver consistent results.
- Advanced weighing systems ensure precise fills.
- Reduce waste caused by errors in measurement.
2. Faster Production
Machines operate at high speeds.
- Handle large volumes efficiently.
- Meet customer demand without delays.
Automatic Filling Machines take speed and consistency to the next level.
3. Lower Labor Costs
Fewer operators are needed.
- Machines handle repetitive tasks.
- Labor savings can be redirected to other areas.
4. Improved Hygiene
Machines are designed to minimize contamination.
- Stainless steel components ensure easy cleaning.
- Enclosed systems reduce exposure to external elements.
5. Scalability
Easily increase production capacity.
- Machines are adaptable to higher outputs.
- Semi-automatic and Automatic Filling Machines cater to growing business needs.
Features That Make Powder Filling Machines Superior
1. Precision Control
- Auger systems ensure smooth powder flow.
- Sensors detect and correct inconsistencies.
2. Customizable Settings
- Adjust fill weights for various powders.
- Compatible with multiple container sizes and shapes.
3. Automated Operations
- Automatic Filling Machines reduce human intervention.
- Continuous operation improves productivity.
4. Built-In Safety Features
- Emergency stop buttons prevent accidents.
- Enclosed hoppers keep operators safe from exposure.
5. Seamless Integration
- Easily integrates with sealing and labeling systems.
- Streamlines the entire packaging process.
Industries Benefiting from Powder Filling Machines
1. Pharmaceuticals
- Accurate dosing ensures regulatory compliance.
- Hygienic designs protect sensitive products.
2. Food and Beverages
- Consistent portioning improves customer satisfaction.
- Machines handle a variety of powders like spices and protein mixes.
3. Cosmetics
- Precise filling minimizes waste of high-cost powders.
- Machines cater to delicate containers.
4. Chemicals
- Safely fills hazardous or abrasive powders.
- Machines maintain accurate measurements for industrial applications.
Each industry gains unique advantages from a Powder Filling Machine.
Advantages of Automatic Filling Machines
Automatic Filling Machines enhance operations with advanced features.
Key Benefits:
- Smart Sensors: Adjust settings in real time for consistent fills.
- Increased Speed: Handles thousands of containers per hour.
- Error Detection: Alerts operators to issues like clogs or misalignments.
- Reduced Human Error: Automation ensures repeatable, accurate results.
Automation is a game-changer for high-volume producers.
Common Myths About Powder Filling Machines
1. Too Expensive
Fact: The initial investment is offset by long-term savings.
- Reduced labor costs and waste make machines cost-effective.
2. Difficult to Maintain
Fact: Modern machines are designed for easy maintenance.
- Follow regular cleaning and inspection routines for optimal performance.
3. Only for Large Businesses
Fact: Machines are available for all scales of production.
- Semi-automatic machines are perfect for small businesses.
Tips for Transitioning to a Powder Filling Machine
1. Assess Production Needs
Determine your output requirements.
- Semi-automatic machines work well for small-scale operations.
- Choose an Automatic Filling Machine for high-volume demands.
2. Train Operators
Provide proper training on machine use.
- Reduces errors during operation.
- Enhances machine efficiency.
3. Choose the Right Features
Match machine capabilities to your product.
- Sticky powders may need specialized augers.
- Free-flowing powders work with simpler systems.
4. Maintain Regularly
Ensure consistent performance with routine maintenance.
- Clean hoppers and nozzles to prevent clogs.
- Inspect components for wear and tear.
Real-World Benefits of Switching
Businesses that switch to Powder Filling Machines report:
- 50% Faster Production Rates: Machines fill containers quicker than manual labor.
- 30% Cost Savings: Reduced labor and waste improve profitability.
- Improved Product Quality: Uniform filling builds trust and brand loyalty.
The numbers show clear benefits for every business.
Future Trends in Powder Filling Machines
Technology continues to improve these machines.
Innovations to Watch:
- IoT Integration: Monitor and control machines remotely.
- AI Features: Predict maintenance needs and optimize performance.
- Eco-Friendly Designs: Energy-efficient machines that support sustainable packaging.
These advancements make Powder Filling Machines even more indispensable.
Switching from manual filling to a Powder Filling Machine is a smart investment for any business. These machines offer unmatched accuracy, speed, and efficiency, making them essential for modern production.
For businesses looking to scale, an Automatic Filling Machine is the ultimate solution. It minimizes human error, reduces costs, and enhances productivity.
By upgrading to a machine that meets your needs, you can achieve long-term success while delivering consistent, high-quality products.