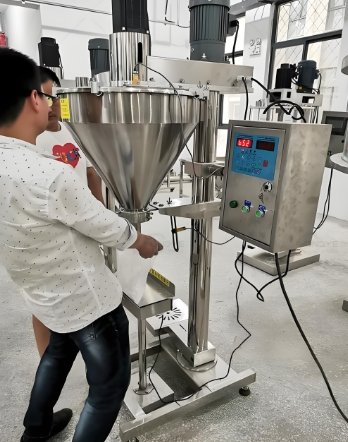
A Powder Filling Machine is crucial for precise packaging in industries like food, pharmaceuticals, and chemicals. Accuracy is key to maintaining product quality and meeting regulatory standards. Understanding the accuracy levels of these machines helps businesses select the right equipment and optimize their production processes.
This article dives into the factors affecting accuracy, how Automatic Filling Machines improve precision, and tips for maintaining accuracy over time.
Why Accuracy Matters
Benefits of Accurate Filling:
- Consistent Product Quality: Ensures each package meets weight standards.
- Reduced Waste: Minimizes overfilling or underfilling.
- Regulatory Compliance: Meets industry requirements for labeling and contents.
- Customer Satisfaction: Builds trust with uniform product delivery.
Accuracy is not just a feature; it’s a necessity in today’s competitive markets.
How Accuracy Levels Are Measured
1. Tolerance Levels
- The acceptable deviation from the target weight.
- Typically expressed as a percentage (e.g., ±1%).
2. Standard Deviation
- Measures the variation between actual and intended fills.
- Lower standard deviation means higher accuracy.
3. Fill Weight Range
- The range within which the machine operates accurately.
- Defined by the machine’s capacity and powder type.
Powder Filling Machines with tighter tolerances deliver better results.
Factors Affecting Accuracy
1. Powder Characteristics
- Free-flowing powders fill more consistently.
- Sticky or clumpy powders may require specialized handling.
2. Machine Type
- Semi-automatic machines rely on operator skill, affecting precision.
- Automatic Filling Machines use advanced sensors for higher accuracy.
3. Container Size and Shape
- Irregular containers can cause misalignment.
- Consistent shapes ensure smoother filling.
4. Environmental Conditions
- Humidity affects powder flow.
- Stable conditions improve performance.
5. Calibration
- Regular calibration ensures accurate measurements.
- Neglecting calibration can lead to errors.
Accuracy Features in Powder Filling Machines
1. Weighing Systems
- Digital scales measure exact amounts.
- Ideal for high-precision requirements.
2. Auger Screw Mechanisms
- Control the flow of powder into containers.
- Adjustable for different powders and fill weights.
3. Sensors and Feedback Loops
- Detect inconsistencies in real time.
- Automatically adjust settings to maintain accuracy.
4. Customizable Settings
- Fine-tune fill speed and weight for specific products.
- Ensure compatibility with diverse powder types.
Automatic Filling Machines integrate these features for seamless accuracy.
Industries Relying on Accurate Powder Filling
1. Pharmaceuticals
- Precise dosing ensures patient safety.
- Errors in fill weight can lead to non-compliance.
2. Food and Beverages
- Consistent portions maintain taste and quality.
- Accuracy is critical for powdered drinks, spices, and baking mixes.
3. Cosmetics
- Exact fills prevent waste of expensive powders.
- Uniformity enhances product presentation.
4. Chemicals
- Precise measurements ensure safety in handling and usage.
- Essential for detergents, fertilizers, and pigments.
Accurate Powder Filling Machines are indispensable in these industries.
How Automatic Filling Machines Improve Accuracy
1. Real-Time Adjustments
- Sensors detect weight discrepancies instantly.
- Machines adjust flow rates to stay within target ranges.
2. Consistent Performance
- Operate at high speeds without sacrificing precision.
- Ensure uniformity across large production runs.
3. Reduced Human Error
- Automation minimizes mistakes during operation.
- Guarantees repeatable results.
4. Advanced Software Integration
- Tracks accuracy metrics for each batch.
- Provides detailed reports to identify and resolve issues.
Common Accuracy Challenges and Solutions
1. Clogged Nozzles
Cause: Residue buildup.
Solution: Clean nozzles regularly to ensure smooth flow.
2. Powder Spillage
Cause: Incorrect alignment or overfilling.
Solution: Adjust settings and check nozzle alignment.
3. Inconsistent Filling
Cause: Calibration errors or worn components.
Solution: Recalibrate the machine and replace faulty parts.
4. Environmental Impact
Cause: Humidity or temperature fluctuations.
Solution: Use dehumidifiers and maintain stable production environments.
Tips for Maintaining Accuracy
1. Clean the Machine Regularly
- Prevent powder residue from affecting performance.
- Focus on hoppers, nozzles, and auger screws.
2. Calibrate Frequently
- Use test weights to ensure correct settings.
- Perform calibration after heavy production runs.
3. Inspect Components
- Check for wear on augers, seals, and weighing systems.
- Replace damaged parts promptly.
4. Train Operators
- Proper training reduces operator errors.
- Ensure staff understand machine settings and functions.
Choosing the Right Machine for Your Accuracy Needs
Key Factors:
1. Production Volume
- For high output, choose an Automatic Filling Machine with advanced features.
- For smaller batches, semi-automatic machines may suffice.
2. Powder Type
- Sticky powders need specialized augers.
- Free-flowing powders work with standard systems.
3. Tolerances
- Select a machine with the tightest tolerances for your industry.
4. Advanced Features
- Look for real-time feedback systems and smart sensors.
Future Trends in Powder Filling Accuracy
Technological advancements are enhancing accuracy levels.
Innovations:
- IoT Integration: Enables remote monitoring and adjustments.
- AI Algorithms: Predict and correct discrepancies before they occur.
- Enhanced Sensors: Provide even tighter tolerances for critical industries.
These advancements ensure Powder Filling Machines remain highly accurate and efficient.
Understanding the accuracy levels of a Powder Filling Machine is essential for optimizing production and maintaining quality. Factors like powder type, machine calibration, and environmental conditions play a significant role. Automatic Filling Machines elevate accuracy with real-time adjustments, advanced sensors, and automation.
By maintaining your machine and choosing the right features, you can reduce waste, improve efficiency, and deliver consistent results. Invest in precision to build a strong, reliable production process.