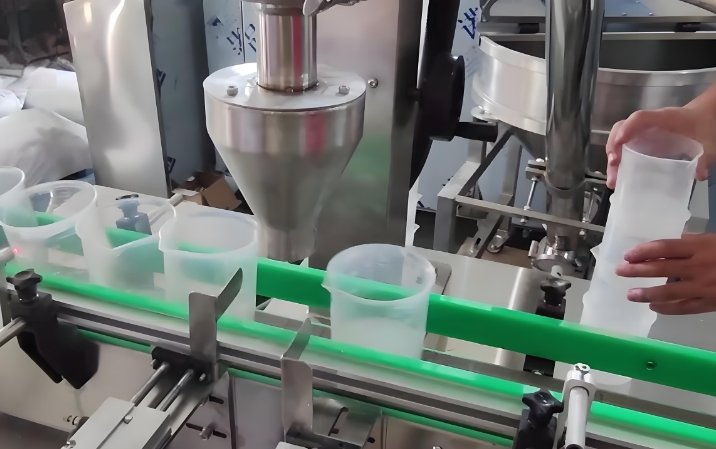
Using a Powder Filling Machine requires caution and strict adherence to safety procedures. Whether it’s a Manual or an Automatic Filling Machine, safety remains a priority. This article provides critical safety tips to help operators prevent accidents, maintain a safe workspace, and ensure efficient machine performance.
1. Read and Follow the Manufacturer’s Guidelines
Each Powder Filling Machine has unique operating instructions. Review these guidelines thoroughly. They provide specific instructions on handling, cleaning, and troubleshooting. Adhering to these directions will prevent common mistakes and increase safety.
Reading the manufacturer’s guidelines ensures operators understand how the machine functions. It includes essential information about machine capacity, compatible powders, and any specific requirements. Misusing a machine due to a lack of knowledge can lead to safety risks.
2. Conduct Routine Inspections
Regular inspections of the Automatic Filling Machine ensure safe operation. Check for any wear or damage on critical parts, including seals, valves, and conveyor belts. Damaged parts can cause malfunctions, leading to accidents or inaccurate filling.
These inspections should include testing the safety features. If a safety guard or emergency stop button malfunctions, repairs should be done immediately. Consistent inspections ensure the machine runs smoothly and safely.
3. Wear Proper Protective Equipment (PPE)
When operating a Powder Filling Machine, always wear PPE, including gloves, safety glasses, and face masks. This equipment protects operators from powder inhalation, skin contact, and eye exposure. Some powders can be harmful if inhaled or touched.
Proper PPE also includes ear protection, as many machines produce high noise levels. Operators need full-body protection to work safely around machines handling fine powders.
4. Ensure Proper Ventilation
Powder particles can become airborne during the filling process. This buildup can create health hazards. Therefore, good ventilation is essential. Proper ventilation helps reduce the risk of inhalation and keeps the air clean.
Some Automatic Filling Machines have built-in ventilation systems. However, additional ventilation may be required in larger facilities. This minimizes dust accumulation, improving both operator safety and machine performance.
5. Train Operators Regularly
Operator training is vital for the safe handling of a Powder Filling Machine. Trained operators are more efficient and alert to potential risks. Training should cover machine functions, troubleshooting, and emergency procedures.
Regular training updates ensure all team members stay informed about the latest safety practices. Properly trained operators can identify issues quickly, preventing potential accidents and ensuring a safe work environment.
6. Use Compatible Powders
Ensure that the Automatic Filling Machine is compatible with the specific powder you intend to fill. Some machines are designed for certain powder types. Using incompatible powders can cause clogs, contamination, or machine malfunctions.
Read the machine’s manual to confirm compatibility with your powder. It’s essential to maintain product quality and avoid costly downtime due to unexpected issues.
7. Maintain Cleanliness
Cleanliness is crucial for powder filling operations. Residual powder buildup can clog the machine, leading to malfunctions or inaccurate filling. After every use, clean the machine thoroughly, including nozzles and hoppers.
Using compressed air to clean certain parts can be effective, but ensure the machine is off before cleaning. Regular cleaning helps prevent contamination and extends the life of the Powder Filling Machine.
8. Test Emergency Stop Functions
Every Automatic Filling Machine has an emergency stop function. Regularly test this function to confirm it works correctly. In an emergency, this button can prevent accidents and protect operators.
Emergency stop functions are usually placed in accessible locations for quick action. Testing them regularly ensures they’re functional, especially if operators need to stop the machine immediately.
9. Avoid Overloading
Each Powder Filling Machine has a specific capacity limit. Overloading can damage the machine and cause safety hazards. Follow the manufacturer’s recommended capacity.
Overloading not only affects machine accuracy but also increases the risk of breakdowns. Regular monitoring of powder levels can prevent this. Respecting capacity limits ensures safe and accurate filling.
10. Use the Correct Power Source
Ensure the machine is connected to the proper power source. An incorrect power supply can damage the machine and increase safety risks. Refer to the manual to verify voltage requirements.
Overloading circuits can lead to power outages and fire hazards. A stable power source ensures the machine operates safely and efficiently.
11. Secure the Work Area
Keeping the workspace around the Powder Filling Machine organized promotes safety. Clear any obstructions and place safety barriers if necessary. This prevents slips and falls, especially when handling large powder quantities.
Safety barriers help control access, reducing risks of accidental machine contact. Ensuring a clear workspace creates a safer environment for both operators and nearby workers.
12. Monitor for Overheating
The Automatic Filling Machine may generate heat during operation. Monitoring for overheating helps prevent potential machine failure. Machines running for extended periods are prone to overheating, which may cause fires or malfunctions.
Inspecting the machine’s temperature sensors can help detect early signs of overheating. Routine checks reduce the chances of unexpected breakdowns and accidents.
13. Use Authorized Replacement Parts
If parts need replacement, use only authorized parts. Generic parts may not fit well and can compromise machine safety. These authorized parts are designed to meet safety standards for specific Powder Filling Machines.
Using genuine parts extends machine life and maintains optimal performance. It also ensures compliance with safety regulations, reducing liability risks.
14. Monitor Humidity Levels
Certain powders may react to humidity, causing clumping or poor flow. High humidity can also lead to machine malfunctions. Ensure the workspace maintains a suitable humidity level to prevent issues.
Humidity control systems can improve air quality, promoting a safer filling process. Keeping humidity levels stable prevents powder quality degradation and improves filling accuracy.
15. Label and Store Powders Properly
Proper powder storage is essential. Label each powder container and store them in a cool, dry place. Mislabeling or poor storage can lead to accidental contamination, affecting the final product quality.
Following these labeling practices maintains powder integrity, ensuring a safer and more efficient filling process. Good storage management reduces waste and contamination risks.
Final Thoughts
Operating a Powder Filling Machine requires strict safety measures. By following these safety tips, companies can reduce risks, protect operators, and maintain efficient production. Proper training, regular inspections, and adherence to manufacturer guidelines all play a role in ensuring safety.
A well-maintained Automatic Filling Machine provides consistent and accurate filling, helping businesses achieve high productivity with minimal risk. Safety is a crucial aspect of every powder filling operation, and taking these steps ensures a safer workplace for all.