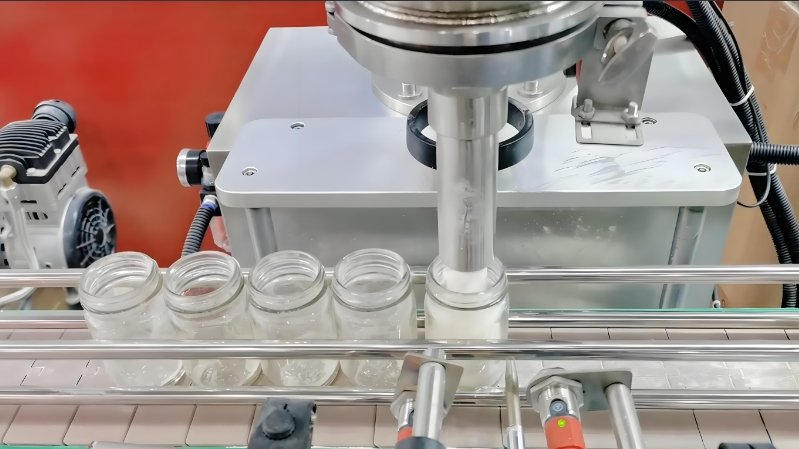
In today’s fast-paced manufacturing world, productivity is essential. Powder Filling Machines play a crucial role in achieving high output in industries like pharmaceuticals, cosmetics, and food production. Designed to streamline the filling of fine powders, these machines can significantly reduce labor costs and time, improving both efficiency and accuracy. In particular, Automatic Filling Machines provide precise, fast, and consistent results, enabling businesses to meet high production demands.
This article explores ways to maximize productivity using Powder Filling Machines. From choosing the right model to implementing best practices, we’ll cover essential strategies to get the most out of these machines.
Choosing the Right Powder Filling Machine
- Analyze Your Product RequirementsDifferent powders have unique characteristics. Some are free-flowing, while others are sticky or clumpy. Choosing a Powder Filling Machine that can handle your specific powder type ensures smooth operation. For example, free-flowing powders work well with auger filling machines. More complex materials may need specialized filling systems.
- Consider Automatic vs. Semi-AutomaticAutomation can be a game-changer. Automatic Filling Machines can process larger volumes quickly, saving time and labor. Semi-automatic machines are useful for smaller operations with lower production needs. Understanding your production scale helps you select the right level of automation to maximize productivity.
- Focus on Machine PrecisionHigh precision in filling minimizes product waste. With Automatic Filling Machines, operators can set exact fill levels. Accurate powder measurement reduces the need for rework or adjustments. Look for machines with adjustable filling systems and real-time monitoring for the best results.
Best Practices for Maximizing Productivity
- Regular Maintenance of Filling MachinesPreventative maintenance is critical. A Powder Filling Machine that’s well-maintained runs smoothly and avoids unexpected breakdowns. Regular cleaning, inspection, and part replacement extend the machine’s life. This reduces downtime and maintains steady production output.
- Optimize Settings for ConsistencyCalibrating your Automatic Filling Machine is essential. By adjusting fill speed, volume, and flow rate, you achieve a consistent fill level. Experimenting with settings helps find the optimal combination that reduces spillage and maximizes accuracy. When settings are fine-tuned, productivity naturally increases.
- Monitor Powder Flow and Fill Levels: Different powders have unique flow properties. Some powders require specific settings for an even fill. Adjust the machine to prevent overflow and spillage. Monitoring and adjusting the powder flow keeps production consistent and reduces waste.
- Implement Safety ProceduresSafety should never be overlooked. Proper safety protocols protect operators and ensure smooth machine operation. For instance, wearing protective equipment and using dust control measures keeps the workspace safe. An organized workspace allows operators to run Automatic Filling Machines efficiently, avoiding potential hazards and delays.
- Train Your Team on Machine UseTraining employees on proper machine operation increases efficiency. When workers understand how to set up, adjust, and maintain the Powder Filling Machine, they prevent minor issues from turning into significant problems. Trained staff also contribute to a faster and more productive production line.
The Advantages of Automatic Powder Filling Machines
- Increased Throughput: Automatic Filling Machines boost production rates. Automated machines can handle high volumes of product in a short time, meeting tight deadlines with ease. Businesses with large production needs benefit from automation as it maximizes throughput and keeps up with market demand.
- Consistent Quality Control: Automated machines offer precise filling with minimal variance, ensuring each product meets the same standard. Powder Filling Machines provide consistent fill levels across every unit. Consistent quality is essential for customer satisfaction, especially in sectors like pharmaceuticals and food.
- Reduced Waste: Automatic Filling Machines allow precise adjustments, minimizing powder loss. Reduced waste is particularly valuable when dealing with costly powders. Setting the machine to an accurate fill level ensures the exact amount of powder is dispensed, saving resources and improving profit margins.
- Lower Labor CostsAutomation reduces reliance on manual labor. With an Automatic Filling Machine, fewer operators are needed to maintain productivity. This lowers labor costs and reduces the risk of human error, which contributes to higher accuracy and efficiency.
- Improved Safety and CleanlinessAutomatic machines often feature enclosed designs, keeping powders contained. This reduces the risk of spills and contamination. For industries where hygiene is essential, like food and cosmetics, Powder Filling Machines provide a cleaner solution.
Key Features to Look for in a Powder Filling Machine
- Adjustable Filling Speeds Adjustable speed allows the machine to handle different powders and container sizes. Look for machines that offer flexibility in filling speed, as this will help optimize production based on product needs.
- Automated Cleaning Systems Some machines feature automatic cleaning options, which save time and maintain a high hygiene standard. Automatic cleaning also reduces labor costs associated with manual cleaning.
- Real-Time Monitoring and Data Tracking Advanced Powder Filling Machines come with digital interfaces for real-time monitoring. These systems track output, fill levels, and any deviations from the set parameters. Data tracking helps identify issues quickly and maintain productivity.
Troubleshooting Common Issues
- Inconsistent Filling LevelsThis issue often arises due to powder flow rate fluctuations. Adjust the powder flow settings on the Automatic Filling Machine. Regular calibration can prevent this problem.
- Powder Leakage or SpillsPowder leakage typically results from incorrect machine settings or improper sealing. Ensure that containers align correctly and adjust the fill speed if necessary. Regular maintenance of seals and valves also helps reduce leakage.
- Machine JamsMachines may jam if powders have a high moisture content or are overly sticky. Properly store and handle powders to prevent moisture buildup. Jams can be reduced by selecting a Powder Filling Machine compatible with the powder’s texture.
- Unresponsive SensorsSensors that don’t respond may need recalibration or cleaning. If the machine uses digital controls, restart the system to resolve minor glitches. Regularly inspect and clean sensors to avoid malfunctions that could disrupt productivity.
Investing in Powder Filling Machines is a strategic choice for businesses looking to maximize productivity. These machines offer speed, accuracy, and consistency, all crucial for high-quality production. When selecting a machine, focus on choosing the right level of automation and maintaining the equipment. With Automatic Filling Machines, companies can achieve optimal output while keeping costs low.
For industries requiring high output and precision, a Powder Filling Machine is an invaluable tool. By applying best practices and focusing on equipment maintenance, businesses can keep production lines running smoothly. Maximize productivity by embracing automation, training employees, and continually monitoring your machine’s performance.