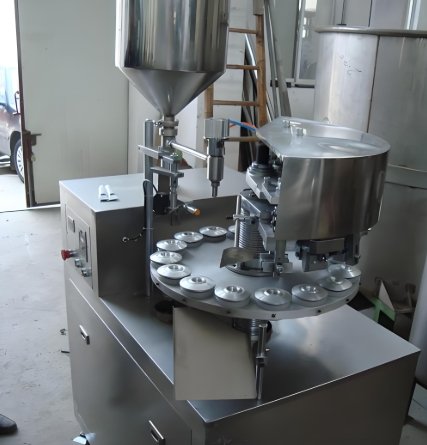
A Tube Filling and Sealing Machine plays a crucial role in modern manufacturing. These machines fill tubes with precision and securely seal them. When combined with an Automatic Filling Machine, they deliver consistent results. They are widely used in industries like cosmetics, pharmaceuticals, and food.
Understanding Tube Filling and Sealing Machines
A Tube Filling and Sealing Machine fills products into tubes and seals them. It handles various materials like plastic, metal, or laminate. It ensures no leaks, making it ideal for liquids, pastes, and gels.
Key Components
Hopper
The hopper stores the product before filling.
Filling System
This part dispenses the exact amount into each tube.
Sealing Mechanism
It seals the tube after filling, ensuring durability.
Control Panel
Operators use this for adjustments.
Conveyor
The conveyor moves tubes through the machine.
The Working Process
Step 1: Tube Loading
The machine automatically loads empty tubes.
Step 2: Product Filling
The Automatic Filling Machine dispenses a precise amount. Sensors ensure accuracy.
Step 3: Sealing
The sealing mechanism closes the tube. It can use heat or ultrasonic technology.
Step 4: Coding
Optional coding units add dates or batch numbers.
Step 5: Ejection
Finished tubes are ejected for packaging.
The Role of Automation
An Automatic Filling Machine makes the process faster. It reduces manual errors. It ensures uniformity in every tube. Automation also increases production capacity.
Applications of Tube Filling and Sealing Machines
Cosmetics
These machines fill lotions, creams, and serums. They provide aesthetic seals for attractive packaging.
Pharmaceuticals
They handle ointments and gels with high precision. This ensures dosage accuracy.
Food and Beverage
Filling sauces, pastes, or spreads is easy. These machines ensure hygiene.
Industrial Products
They are used for adhesives, lubricants, and chemicals. Strong seals protect the products during transport.
Benefits of Using These Machines
High Precision
They ensure every tube has the exact amount.
Speed
The Automatic Filling Machine significantly boosts production speed.
Versatility
They handle multiple tube sizes and materials.
Cost Savings
Automation reduces labor costs and product wastage.
Enhanced Hygiene
Sealed systems prevent contamination.
Innovations in Tube Filling and Sealing Machines
Modern machines have advanced features. Touchscreens allow easy control. Sensors detect errors and halt operations. Energy-efficient models reduce power consumption.
Maintenance Tips
- Regularly clean the hopper and filling system.
- Inspect seals and moving parts for wear.
- Lubricate mechanical components.
- Follow the manufacturer’s maintenance schedule.
Choosing the Right Machine
Consider Your Product
Choose a machine that suits your product’s viscosity.
Tube Material Compatibility
Ensure the machine can handle your tube materials.
Production Scale
Pick a machine that matches your output requirements.
Automation Level
An Automatic Filling Machine is ideal for high-volume operations.
Industries That Rely on These Machines
Small Businesses
Compact models help startups achieve professional packaging.
Large Factories
High-speed models meet large-scale demands.
Specialized Industries
Customizable machines cater to unique product needs.
Why Invest in Automation?
Automation reduces manual intervention. It ensures consistent quality. It also helps meet tight production deadlines. An Automatic Filling Machine is a must for efficient manufacturing.
Challenges and Solutions
Issue: Product Overflow
Solution: Adjust the filling nozzle for better accuracy.
Issue: Weak Seals
Solution: Check the sealing temperature settings.
Issue: Tube Misalignment
Solution: Inspect and calibrate the conveyor system.
A Tube Filling and Sealing Machine is an essential tool. It ensures precise filling and strong sealing. Paired with an Automatic Filling Machine, it improves efficiency. These machines are ideal for diverse industries. Investing in one guarantees high-quality results and reliable operations.