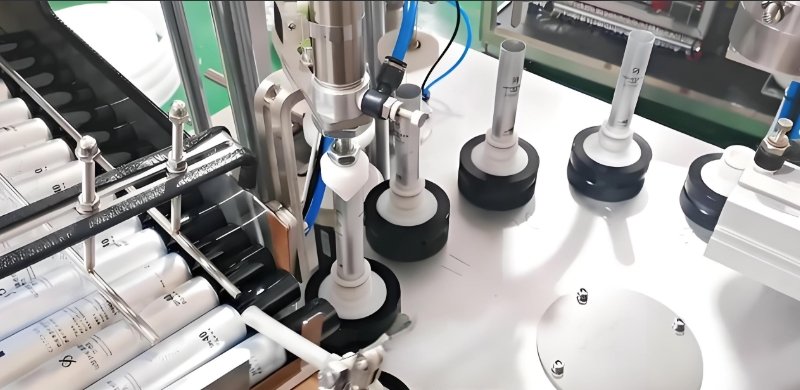
A Tube Filling and Sealing Machine is vital for efficient production. Proper maintenance ensures consistent performance. It also prolongs the machine’s life. When paired with an Automatic Filling Machine, efficiency improves. Here’s how to maintain these machines effectively.
Why Maintenance Matters
Regular maintenance prevents breakdowns. It keeps production smooth. It reduces downtime and saves money. Neglected machines lead to costly repairs.
Daily Maintenance
1. Clean the Machine
Dirt and residue build up daily. Clean the hopper and filling parts. Wipe the sealing components carefully. Use mild cleaning agents to avoid damage.
2. Inspect the Seals
Check the sealing components. Look for wear or cracks. Replace worn seals immediately.
3. Check Lubrication
Ensure moving parts are well-lubricated. Lack of lubrication increases friction. This damages components over time.
4. Test the Sensors
Sensors control precision. Ensure they are aligned correctly. Misaligned sensors cause errors.
Weekly Maintenance
1. Inspect for Wear
Check all parts for wear and tear. Focus on seals, nozzles, and motors. Replace damaged parts promptly.
2. Tighten Loose Screws
Machines vibrate during operation. This can loosen screws. Tighten them regularly to prevent further damage.
3. Verify Calibration
Calibration ensures accurate filling. Test the machine’s settings weekly. Adjust as needed for consistency.
4. Monitor Temperature Controls
Sealing requires precise temperatures. Check the heater regularly. Ensure it reaches the required heat.
Monthly Maintenance
1. Deep Clean
Perform a deep cleaning once a month. Remove all parts that handle products. Wash them thoroughly.
2. Inspect the Electrical System
Electrical faults cause downtime. Check all wires and connections. Look for signs of wear or damage.
3. Test Machine Performance
Run a test batch monthly. Observe the machine’s speed and accuracy. Address any irregularities.
4. Review Automation Features
If paired with an Automatic Filling Machine, test the automation system. Ensure it integrates smoothly with the tube filler.
Preventive Maintenance Tips
1. Create a Schedule
Set a regular maintenance schedule. Assign tasks to trained operators. Follow the schedule strictly.
2. Use Genuine Parts
Always use parts recommended by the manufacturer. Generic parts may not fit well. This can lead to further damage.
3. Train Operators
Properly trained operators handle the machine better. They also identify issues early. Invest in regular training.
4. Keep a Spare Parts Inventory
Stock up on essential spare parts. This reduces downtime during repairs.
Common Issues and How to Fix Them
1. Irregular Filling
If the machine fills unevenly, check the nozzles. Clean them thoroughly. Test the calibration settings.
2. Poor Sealing
Check the heater and sealing jaws. Ensure the temperature is accurate. Replace worn sealing parts.
3. Slow Performance
Inspect the motor and drive system. Lubricate moving parts. Test the automation system for delays.
4. Leaking Tubes
Leaks indicate sealing issues. Inspect the sealing components. Replace any damaged parts immediately.
Maintenance for Automatic Filling Machines
Paired Automatic Filling Machines also need care. Follow these tips:
- Clean the filling nozzles daily.
- Lubricate the conveyor system.
- Test the automation features weekly.
- Inspect the control panel regularly.
These steps ensure smooth integration with the Tube Filling and Sealing Machine.
Advanced Maintenance
1. Professional Servicing
Hire professionals for annual servicing. They identify hidden issues. They also ensure all parts function correctly.
2. Upgrade Software
Modern machines use advanced software. Update it regularly. This improves efficiency and adds new features.
3. Check Air Pressure
Machines that use pneumatic systems need proper air pressure. Test the air supply regularly. Adjust if needed.
4. Inspect Bearings
Bearings endure heavy loads. Check them for wear. Replace them if necessary.
Benefits of Proper Maintenance
- Longer Machine Life: Proper care extends lifespan.
- Higher Efficiency: Well-maintained machines work faster.
- Reduced Downtime: Preventive care minimizes repairs.
- Better Product Quality: Consistency improves with regular maintenance.
Maintenance Checklist
Daily
- Clean hopper and seals.
- Lubricate moving parts.
- Test sensors.
Weekly
- Tighten screws.
- Inspect nozzles and seals.
- Verify calibration.
Monthly
- Perform deep cleaning.
- Check electrical systems.
- Test automation features.
A Tube Filling and Sealing Machine is a valuable asset. Paired with an Automatic Filling Machine, it boosts efficiency. Regular maintenance ensures peak performance. Follow these tips to keep your machine in top shape.
Invest in proper care. It saves money and improves production. Your machine will serve you well for years to come.