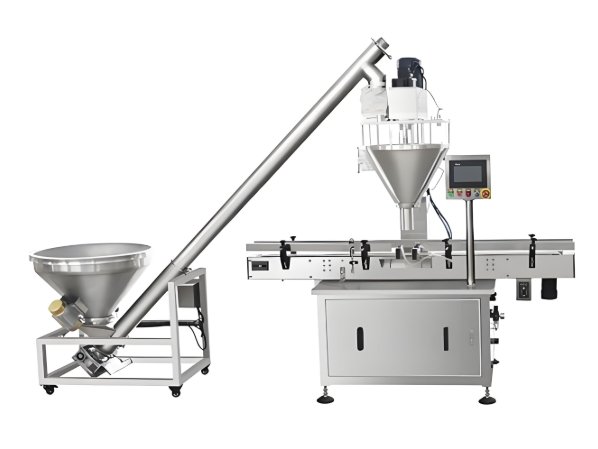
High-volume producers face unique challenges. They must maintain accuracy, speed, and efficiency to meet demand. A Powder Filling Machine is a vital tool in achieving these goals. It streamlines the process of filling powdered products, reducing waste and ensuring consistency.
For large-scale operations, an Automatic Filling Machine offers unmatched productivity. This article explores how these machines benefit high-volume producers, highlighting their features and advantages.
The Role of Powder Filling Machines in High-Volume Production
Why They Are Essential
- Efficiency: Increases output without compromising quality.
- Accuracy: Ensures consistent filling across all units.
- Cost-Effectiveness: Reduces waste and labor expenses.
- Scalability: Handles growing production demands.
A Powder Filling Machine is indispensable for large-scale operations.
Features of Powder Filling Machines for High-Volume Producers
1. High-Speed Operation
- Designed to fill large quantities quickly.
- Ideal for meeting tight deadlines.
2. Precision Filling
- Advanced weighing systems ensure accurate measurements.
- Prevents overfilling and underfilling.
3. Automation
- Automatic Filling Machines reduce the need for manual intervention.
- Streamlines the entire production process.
4. Durability
- Built with high-quality materials to handle continuous use.
- Resistant to wear and tear.
5. Flexibility
- Compatible with various powder types and container sizes.
- Easily adjustable for different production requirements.
Benefits for High-Volume Producers
1. Increased Productivity
A Powder Filling Machine works faster than manual methods.
- Handles thousands of units per hour.
- Ensures consistent output during peak production times.
2. Improved Accuracy
Precision is critical in high-volume operations.
- Machines measure powder accurately to meet weight standards.
- Reduces the risk of product recalls due to incorrect filling.
3. Reduced Labor Costs
Automatic Filling Machines minimize the need for manual labor.
- Fewer operators are needed to oversee production.
- Savings can be redirected to other areas of the business.
4. Enhanced Quality Control
Machines ensure uniformity in every package.
- Builds trust with customers.
- Meets regulatory standards consistently.
5. Scalable Solutions
- Machines can adapt to growing production needs.
- Easily upgradeable for higher output.
How Automatic Filling Machines Outperform Manual Processes
Manual filling is time-consuming and error-prone.
Advantages of Automation:
- Speed: Operates continuously without breaks.
- Consistency: Delivers identical results every time.
- Integration: Works seamlessly with other automated systems.
- Monitoring: Smart sensors detect and correct issues in real-time.
For high-volume producers, an Automatic Filling Machine is the ultimate solution.
Industries That Benefit from High-Volume Powder Filling
1. Pharmaceuticals
- Precise filling of medicines and supplements.
- Ensures dosage accuracy and compliance.
2. Food and Beverages
- Handles powders like protein mixes, spices, and instant drinks.
- Maintains freshness and consistency.
3. Cosmetics
- Fills powders for makeup and skincare products.
- Reduces waste of expensive materials.
4. Chemicals
- Efficiently fills detergents, fertilizers, and pigments.
- Improves safety by reducing manual handling.
Common Challenges in High-Volume Production
1. Inconsistent Filling
Cause: Improper calibration or worn components.
Solution: Regular maintenance and calibration.
2. Powder Spillage
Cause: Overfilling or misaligned nozzles.
Solution: Adjust machine settings and check alignment.
3. Downtime
Cause: Mechanical failures.
Solution: Invest in durable machines and conduct routine inspections.
4. Powder Contamination
Cause: Poor cleaning practices.
Solution: Implement strict cleaning protocols.
Maintenance Tips for Long-Term Efficiency
1. Regular Cleaning
- Remove powder residues to prevent clogs.
- Focus on hoppers, nozzles, and auger screws.
2. Lubrication
- Use food-safe lubricants for moving parts.
- Reduces friction and prolongs machine lifespan.
3. Component Inspections
- Check for wear and tear on critical parts.
- Replace damaged components promptly.
4. Calibration
- Ensure accurate filling by recalibrating regularly.
- Perform tests before large production runs.
Tips for Choosing the Right Powder Filling Machine
1. Consider Production Volume
- Choose a machine that matches your current and future needs.
- For large-scale production, opt for an Automatic Filling Machine.
2. Assess Powder Characteristics
- Sticky powders require specialized augers.
- Free-flowing powders work with standard systems.
3. Check Machine Features
- Look for high-speed operation and precision controls.
- Ensure compatibility with your containers and powders.
4. Evaluate Maintenance Requirements
- Select machines with easy-to-clean designs.
- Ensure access to spare parts and technical support.
Future Trends in Powder Filling Machines
Innovations are transforming the industry.
1. IoT Integration
- Remote monitoring for real-time updates.
- Detect issues before they cause downtime.
2. AI-Powered Systems
- Optimize machine performance automatically.
- Predict maintenance needs to prevent failures.
3. Sustainability Features
- Energy-efficient designs.
- Support for eco-friendly packaging solutions.
These advancements make machines smarter and more reliable.
For high-volume producers, a Powder Filling Machine is a critical investment. It improves efficiency, accuracy, and scalability. Automatic Filling Machines take these benefits further, offering unparalleled speed and precision.
By choosing the right machine and maintaining it regularly, businesses can meet growing demand while ensuring product quality. Invest in advanced technology to stay ahead in competitive markets.