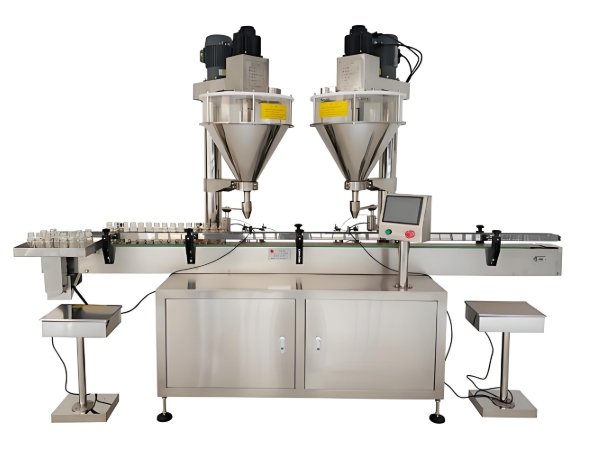
A Powder Filling Machine is vital for precise and efficient packaging of powdered products. Regular maintenance ensures its longevity and reliable performance. Poor upkeep can lead to inaccuracies, breakdowns, and costly repairs.
This article provides essential maintenance tips to keep your Powder Filling Machine and Automatic Filling Machine in top condition. By following these steps, you can reduce downtime, improve productivity, and extend the machine’s lifespan.
Why Maintenance Matters
Key Benefits of Proper Maintenance:
- Improved Efficiency: Ensures smooth operations.
- Consistent Accuracy: Maintains filling precision.
- Reduced Downtime: Prevents unexpected failures.
- Cost Savings: Avoids expensive repairs and replacements.
Neglecting maintenance can compromise performance and product quality.
Essential Maintenance Tips for Powder Filling Machines
1. Regular Cleaning
Cleanliness is crucial for maintaining a Powder Filling Machine.
Steps:
- Clean hoppers, nozzles, and augers after each use.
- Remove powder residue to prevent clogs.
- Use soft brushes and approved cleaning agents.
Benefits:
- Ensures hygienic operations.
- Prevents contamination of products.
2. Inspect Components Frequently
Regular inspections identify potential issues early.
Focus Areas:
- Auger Screw: Check for wear and damage.
- Nozzles: Inspect for blockages.
- Conveyors: Ensure belts are aligned and functioning.
Benefits:
- Reduces the risk of breakdowns.
- Extends the life of critical parts.
3. Lubricate Moving Parts
Proper lubrication minimizes wear and tear.
Tips:
- Use food-grade lubricants if applicable.
- Lubricate gears, bearings, and other moving components.
- Follow the manufacturer’s guidelines for frequency.
Benefits:
- Reduces friction and overheating.
- Ensures smooth operation.
4. Calibrate Regularly
Calibration is essential for accurate filling.
Steps:
- Test the machine before each production run.
- Adjust settings based on powder type and weight.
- Use calibration weights for precise adjustments.
Benefits:
- Maintains consistent filling volumes.
- Reduces product wastage.
5. Replace Worn Parts Promptly
Delaying repairs can cause more damage.
Tips:
- Keep a stock of spare parts like augers and nozzles.
- Replace worn seals and gaskets to maintain airtight systems.
- Monitor sensor performance in Automatic Filling Machines.
Benefits:
- Prevents major failures.
- Keeps production running smoothly.
6. Monitor Electrical Components
Electrical issues can disrupt machine operations.
Focus Areas:
- Check the control panel for loose connections.
- Inspect wiring for signs of wear or damage.
- Ensure sensors and displays work correctly.
Benefits:
- Avoids sudden power failures.
- Ensures safety during operation.
Maintenance for Automatic Filling Machines
Automatic Filling Machines have advanced features that require extra care.
Key Areas:
- Sensors: Clean and recalibrate regularly.
- Automation Software: Update to the latest version.
- Smart Systems: Monitor performance through integrated diagnostics.
Additional Tips:
- Train operators to use automation features correctly.
- Schedule professional servicing for complex systems.
Common Maintenance Challenges and Solutions
1. Powder Residue Build-Up
Cause: Inadequate cleaning.
Solution: Establish a strict cleaning schedule.
2. Inconsistent Filling
Cause: Calibration errors or worn parts.
Solution: Recalibrate and replace damaged components.
3. Nozzle Clogging
Cause: Sticky powders or moisture.
Solution: Clean nozzles frequently and use anti-clogging designs.
4. Machine Overheating
Cause: Lack of lubrication.
Solution: Lubricate all moving parts as per the manual.
Best Practices for Long-Term Maintenance
- Follow the Manual: Adhere to the manufacturer’s maintenance guidelines.
- Schedule Regular Checks: Perform weekly and monthly inspections.
- Document Maintenance Activities: Keep records of repairs and servicing.
- Invest in Quality Parts: Use original components for replacements.
These practices ensure your Powder Filling Machine remains reliable and efficient.
Signs That Your Machine Needs Maintenance
Watch Out For:
- Unusual Noises: Indicates worn gears or bearings.
- Inconsistent Filling: Suggests calibration issues.
- Frequent Downtime: Points to neglect or component failure.
- Powder Leakage: Signals misalignment or damaged parts.
Addressing these signs promptly prevents bigger issues.
The Importance of Professional Servicing
While regular maintenance can be done in-house, professional servicing is essential.
Benefits:
- Thorough Inspections: Experts identify hidden issues.
- Advanced Repairs: Technicians handle complex systems.
- Optimized Performance: Ensures your machine works at peak efficiency.
Schedule servicing for your Automatic Filling Machine at least once a year.
Maintaining a Powder Filling Machine is essential for ensuring reliable performance and long-term efficiency. Regular cleaning, lubrication, and calibration are key to avoiding downtime and costly repairs. Automatic Filling Machines require special attention to their advanced features.
By following these maintenance tips, you can maximize productivity, ensure product quality, and extend the life of your equipment. Prioritize proper care to keep your production running smoothly.