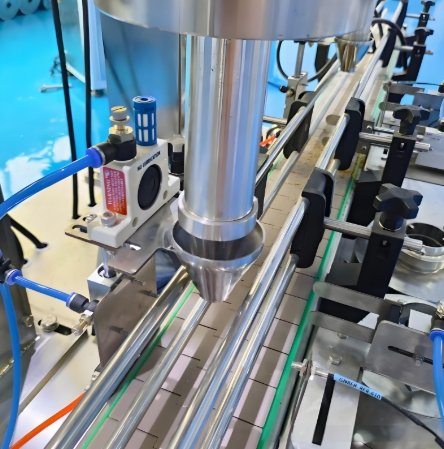
A Powder Filling Machine is vital for industries handling powdered products. Its performance depends on various components working together. Each part plays a specific role, ensuring precision, efficiency, and reliability.
This article explores the essential components of powder filling machines, their functions, and the benefits they bring to production. We’ll also look at how Automatic Filling Machines enhance these features for faster, more accurate results.
Why Understanding Components Is Important
Knowing the parts of a Powder Filling Machine helps in:
- Ensuring proper maintenance.
- Optimizing performance.
- Identifying and fixing issues.
- Selecting the right machine for your needs.
Each component contributes to the overall efficiency of the machine.
Key Components of Powder Filling Machines
1. Hopper
The hopper stores the powder before filling.
Functions:
- Ensures a steady flow of powder.
- Reduces interruptions during filling.
Maintenance Tips:
- Clean after every use to prevent residue buildup.
- Inspect for cracks or leaks.
2. Filling Nozzle
The nozzle directs the powder into containers.
Functions:
- Ensures precise placement of powder.
- Prevents spillage and wastage.
Maintenance Tips:
- Check for clogs regularly.
- Replace worn or damaged nozzles promptly.
3. Auger Screw
The auger screw is crucial for controlling powder flow.
Functions:
- Dispenses powder in accurate amounts.
- Handles various powder types, including sticky or free-flowing powders.
Maintenance Tips:
- Inspect for wear and tear frequently.
- Lubricate to ensure smooth operation.
4. Control Panel
The control panel is the brain of the Powder Filling Machine.
Functions:
- Adjusts filling speed and volume.
- Monitors the machine’s performance.
Maintenance Tips:
- Keep it dust-free.
- Ensure electrical connections are secure.
5. Conveyor System
The conveyor moves containers under the filling nozzle.
Functions:
- Ensures consistent alignment for accurate filling.
- Increases efficiency in high-volume production.
Maintenance Tips:
- Lubricate moving parts regularly.
- Align the conveyor belt to prevent misplacement of containers.
6. Weighing System
The weighing system ensures the correct amount of powder is filled.
Functions:
- Provides real-time weight measurements.
- Ensures compliance with weight regulations.
Maintenance Tips:
- Calibrate the system frequently.
- Inspect sensors for accuracy.
7. Sealing System (Optional)
Some machines include a sealing system for packaging.
Functions:
- Seals containers after filling.
- Maintains product freshness.
Maintenance Tips:
- Check seals for uniformity.
- Replace worn sealing components.
How Automatic Filling Machines Enhance These Components
1. Automation for Efficiency
An Automatic Filling Machine streamlines the entire process.
- Automatically adjusts filling speed and volume.
- Reduces human intervention.
2. Smart Sensors
Advanced machines include sensors that:
- Detect powder flow issues.
- Halt operations if a problem occurs.
3. Faster Conveyor Systems
Automatic Filling Machines have optimized conveyors for high-speed production.
- Suitable for large-scale operations.
- Ensures consistent alignment at higher speeds.
Benefits of a Well-Maintained Powder Filling Machine
Properly maintained components ensure:
- Efficiency: Smooth operation with minimal downtime.
- Accuracy: Consistent filling across all batches.
- Longevity: Extended lifespan of the machine.
- Cost Savings: Reduces repair and replacement costs.
Common Issues with Components and Their Solutions
1. Clogged Nozzles
Cause: Powder residue buildup.
Solution: Clean the nozzle after every use.
2. Irregular Filling
Cause: Calibration errors or worn auger screws.
Solution: Recalibrate and replace damaged parts.
3. Conveyor Misalignment
Cause: Loose or damaged belts.
Solution: Realign and tighten the conveyor system.
4. Weighing Inaccuracy
Cause: Faulty sensors.
Solution: Inspect and recalibrate the weighing system.
Tips for Maintaining Powder Filling Machine Components
1. Regular Cleaning
- Clean hoppers, nozzles, and conveyors after each use.
- Prevents contamination and clogs.
2. Lubrication
- Apply food-grade lubricants to moving parts.
- Reduces friction and wear.
3. Inspection and Repairs
- Check components for damage regularly.
- Replace worn parts promptly.
4. Calibration
- Ensure accurate measurements by recalibrating sensors and scales.
- Perform checks after heavy usage.
Choosing the Right Powder Filling Machine
Key Factors to Consider:
1. Powder Type
- Choose machines with augers for sticky powders.
- Opt for gravity-fed systems for free-flowing powders.
2. Production Volume
- Use semi-automatic machines for small batches.
- Opt for Automatic Filling Machines for high-volume production.
3. Container Size
- Ensure compatibility with your container dimensions.
4. Ease of Maintenance
- Select machines with accessible components for easy cleaning and repairs.
Every component in a Powder Filling Machine plays a critical role in ensuring accuracy, efficiency, and reliability. From the hopper to the control panel, maintaining these parts is essential for smooth operations. Automatic Filling Machines take these features further by streamlining processes and enhancing productivity.
Investing in a high-quality machine and following a strict maintenance schedule ensures consistent performance and long-term success.