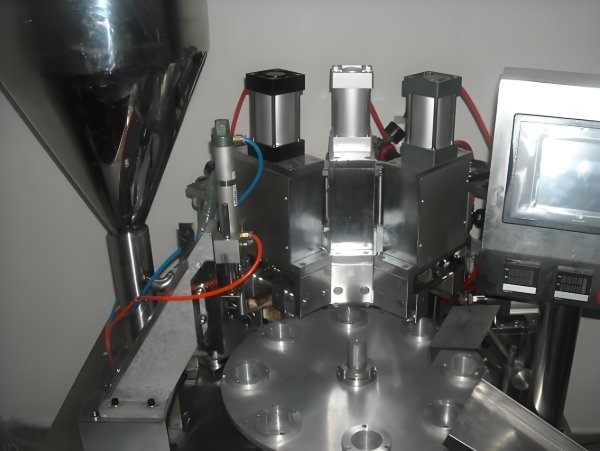
A Tube Filling and Sealing Machine streamlines packaging processes. It pairs well with an Automatic Filling Machine for seamless operations. However, these machines can face challenges. Understanding common problems helps maintain efficiency.
Problem 1: Uneven Product Filling
Uneven filling is a frequent issue. It leads to inconsistent product quantities in tubes.
Causes
- Incorrect settings on the Automatic Filling Machine.
- Blocked or damaged filling nozzles.
- Faulty product sensors.
Solutions
- Adjust the filling volume settings.
- Clean and inspect the filling nozzles regularly.
- Replace faulty sensors immediately.
Problem 2: Poor Tube Sealing
Seal failures compromise the product’s quality.
Causes
- Incorrect sealing temperature.
- Misaligned tubes.
- Worn-out sealing jaws.
Solutions
- Calibrate the sealing temperature.
- Realign the tubes before starting the process.
- Replace worn-out components.
Problem 3: Tube Misalignment
Misaligned tubes disrupt the workflow. It may cause filling and sealing errors.
Causes
- Faulty tube holders.
- Vibrations during operation.
- Inadequate machine calibration.
Solutions
- Inspect and adjust tube holders.
- Reduce operational vibrations.
- Calibrate the machine frequently.
Problem 4: Product Leakage
Leaks result in product wastage and messes.
Causes
- Overfilled tubes.
- Improper sealing pressure.
- Damaged tubes.
Solutions
- Reduce the filling volume on the Automatic Filling Machine.
- Increase sealing pressure as needed.
- Use high-quality, undamaged tubes.
Problem 5: Machine Jams
Jams slow down production. They can also damage machine components.
Causes
- Foreign objects in the machine.
- Overloaded product hopper.
- Poor maintenance.
Solutions
- Clean the machine to remove foreign objects.
- Avoid overloading the hopper.
- Follow a strict maintenance schedule.
Problem 6: Sensor Malfunctions
Sensors are crucial for precision. Malfunctions lead to errors.
Causes
- Dirt on sensor lenses.
- Damaged wires.
- Outdated firmware.
Solutions
- Clean sensor lenses regularly.
- Replace damaged wires.
- Update the machine’s firmware.
Problem 7: Inconsistent Tube Trimming
Rough edges or untrimmed tubes look unprofessional.
Causes
- Dull cutting blades.
- Misaligned trimming mechanism.
- Faulty trimming settings.
Solutions
- Sharpen or replace cutting blades.
- Align the trimming mechanism correctly.
- Adjust trimming settings for precision.
Problem 8: Downtime Due to Overheating
Overheating damages internal components. It causes delays and increases costs.
Causes
- Prolonged use without cooling breaks.
- Faulty cooling systems.
- Dust accumulation in vents.
Solutions
- Allow cooling periods during extended operations.
- Repair or replace the cooling system.
- Clean the machine vents often.
Problem 9: Noisy Operations
Excessive noise indicates internal issues.
Causes
- Loose components.
- Insufficient lubrication.
- Damaged motor parts.
Solutions
- Tighten all loose parts.
- Lubricate moving components.
- Replace damaged motor parts.
Problem 10: High Energy Consumption
Some machines consume more energy than expected.
Causes
- Outdated equipment.
- Inefficient motor systems.
- Overworked components.
Solutions
- Upgrade to an energy-efficient model.
- Replace motors with efficient alternatives.
- Service components regularly.
How to Prevent Problems
Prevention is key to long-term efficiency.
Regular Maintenance
- Inspect machines daily.
- Schedule routine servicing.
Operator Training
- Train staff to operate the Tube Filling and Sealing Machine.
- Teach them to troubleshoot basic issues.
Use Quality Materials
- Choose high-quality tubes.
- Use reliable products for filling.
Benefits of a Well-Maintained Machine
Improved Efficiency
Fewer breakdowns mean consistent output.
Cost Savings
Maintenance reduces repair and replacement costs.
Better Product Quality
Properly maintained machines ensure uniform packaging.
Why Pair with an Automatic Filling Machine?
The Automatic Filling Machine complements the sealing process. It improves filling speed and precision. Combined, these machines deliver optimal results.
Key Advantages
- Faster production times.
- Minimal manual intervention.
- Higher filling accuracy.
A Tube Filling and Sealing Machine is essential for efficient production. Pairing it with an Automatic Filling Machine enhances results. However, common problems can hinder operations.
Identifying and solving these issues quickly is vital. Regular maintenance and quality materials help prevent problems. A well-maintained machine saves time and money. It ensures high-quality packaging every time.
Invest in proper care for your machines today. Watch your business grow with reliable and efficient tools.