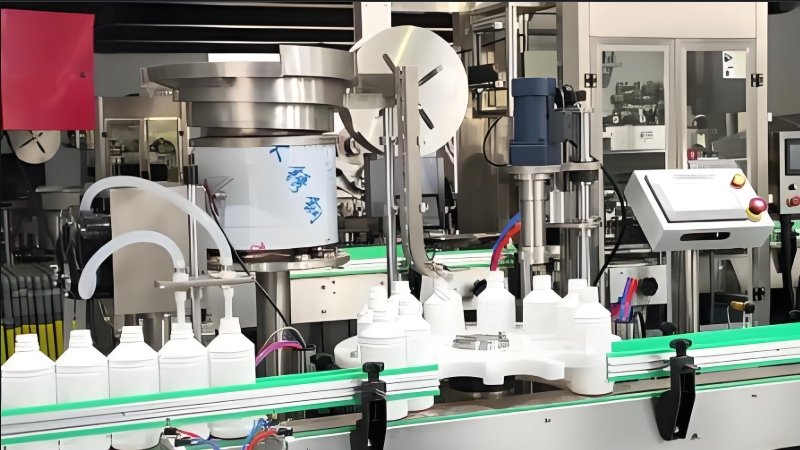
Fine powders require specialized handling during the filling process. Their light, airy nature makes them prone to spillage, dusting, and inconsistencies. A Powder Filling Machine designed for fine powders ensures precision, efficiency, and cleanliness.
This article explores the top Powder Filling Machines for fine powders, their features, and why Automatic Filling Machines are the ideal choice for high-performance operations.
Challenges of Filling Fine Powders
1. Dust Generation
Fine powders easily become airborne.
- Causes waste.
- Risks contamination of the work environment.
2. Inconsistent Flow
Fine powders may clump or flow irregularly.
- Impacts fill accuracy.
- Can clog machine components.
3. Static Electricity
Fine particles generate static during handling.
- Causes powders to stick to surfaces.
- Reduces filling speed and efficiency.
4. Container Compatibility
Fine powders often require specific container types.
- Irregular container designs pose challenges.
A Powder Filling Machine must address these challenges to ensure smooth operation.
Features to Look for in Powder Filling Machines for Fine Powders
1. Advanced Dust Control
- HEPA filters minimize airborne particles.
- Enclosed filling systems prevent contamination.
2. Precision Weighing Systems
- Digital load cells for accurate measurements.
- Consistent fill weights reduce waste.
3. Auger Fillers
- Ideal for fine, non-free-flowing powders.
- Controls powder flow precisely.
4. Vibratory Systems
- Helps powders settle evenly in containers.
- Ensures uniform fills.
5. Customizable Speed Settings
- Adjustable speeds handle varying powder properties.
- Prevents clogging and spillage.
Machines with these features deliver excellent results with fine powders.
Top Powder Filling Machines for Fine Powders
1. Auger-Based Powder Filling Machines
Features:
- Equipped with auger screws for smooth powder flow.
- Suitable for powders prone to clumping.
- Handles a wide range of container sizes.
Benefits:
- High precision in fill weights.
- Minimal powder wastage.
An Automatic Filling Machine with auger technology enhances efficiency and accuracy.
2. Vacuum Powder Filling Machines
Features:
- Uses vacuum technology to handle ultra-light powders.
- Eliminates dust during the filling process.
Benefits:
- Ideal for pharmaceutical and cosmetic powders.
- Prevents contamination and maintains cleanliness.
These machines are perfect for handling delicate and sensitive materials.
3. Multi-Nozzle Filling Machines
Features:
- Multiple nozzles for simultaneous filling.
- Adjustable nozzle sizes for various containers.
Benefits:
- Increases production speed.
- Reduces downtime between container changes.
Multi-nozzle systems are ideal for high-volume operations.
4. Gravity-Fed Powder Filling Machines
Features:
- Simple mechanism for free-flowing fine powders.
- Minimal moving parts reduce maintenance needs.
Benefits:
- Cost-effective for small-scale operations.
- Suitable for powders like flour and talcum.
While not as versatile, gravity-fed systems work well for specific powder types.
Advantages of Automatic Filling Machines for Fine Powders
Automatic Filling Machines offer advanced features that simplify handling fine powders.
Key Benefits:
1. Real-Time Adjustments
- Sensors monitor powder flow.
- Machines automatically adjust to maintain precision.
2. Continuous Operation
- Handles large batches without stopping.
- Ensures consistent output for high-demand industries.
3. Enclosed Systems
- Minimize dust exposure.
- Enhance safety and hygiene.
4. Error Detection
- Detect clogs or weight inconsistencies.
- Alerts operators to resolve issues quickly.
Automation ensures reliable performance for delicate materials.
Industries That Use Powder Filling Machines for Fine Powders
1. Pharmaceuticals
- Handles powdered medicines and supplements.
- Ensures precise dosages for regulatory compliance.
2. Food and Beverages
- Fills protein powders, spices, and baking ingredients.
- Prevents contamination for food-grade products.
3. Cosmetics
- Fills powders for makeup and skincare.
- Reduces waste of expensive materials.
4. Chemicals
- Handles fine powders like pigments and fertilizers.
- Maintains safety during handling.
A Powder Filling Machine is tailored to meet specific industry needs.
Maintenance Tips for Machines Handling Fine Powders
1. Clean Thoroughly
- Remove powder residues to prevent clogs.
- Use compressed air for hard-to-reach areas.
2. Inspect Components
- Check auger screws, nozzles, and seals for wear.
- Replace damaged parts immediately.
3. Calibrate Regularly
- Adjust weight settings for accurate fills.
- Test with sample batches to ensure precision.
4. Lubricate Moving Parts
- Use approved lubricants to reduce friction.
- Prevent wear from prolonged use.
Routine maintenance ensures consistent performance.
How to Choose the Best Powder Filling Machine
Key Factors:
1. Powder Type
- Sticky powders require auger-based systems.
- Free-flowing powders work with gravity-fed machines.
2. Production Volume
- For large-scale operations, choose an Automatic Filling Machine.
- Small batches can use semi-automatic systems.
3. Accuracy Requirements
- Select machines with tight tolerances for precise fills.
4. Budget
- Invest in advanced features if handling sensitive powders.
Matching your needs ensures optimal performance.
Future Trends in Powder Filling Machines
Technology is advancing rapidly for Powder Filling Machines.
Innovations to Watch:
1. AI Integration
- Machines that learn powder behavior and adjust automatically.
2. Eco-Friendly Features
- Energy-efficient designs reduce operational costs.
3. IoT Connectivity
- Real-time monitoring for remote troubleshooting.
These advancements make machines even more effective for fine powders.
Handling fine powders requires specialized equipment. A Powder Filling Machine designed for delicate materials ensures precision, reduces waste, and improves efficiency. Automatic Filling Machines offer advanced features like real-time adjustments, enclosed systems, and continuous operation, making them ideal for high-demand applications.
By investing in the right machine and maintaining it properly, businesses can optimize production and meet the challenges of handling fine powders with ease.