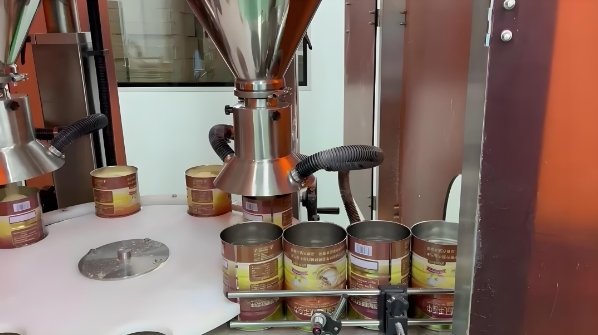
A Powder Filling Machine is a vital asset in many industries, from pharmaceuticals to food production. Regular maintenance can keep it running smoothly for years. Automatic Filling Machines require specific care to prevent breakdowns. Proper maintenance extends machine life, reduces downtime, and minimizes repair costs.
In this guide, we’ll discuss essential maintenance practices for powder filling machines. Simple yet consistent steps help ensure efficiency and durability.
1. Regular Cleaning
Cleaning is essential for a Powder Filling Machine. Patches of dust and residual powder can clog and damage the equipment. Regular cleaning keeps the machine free of powder buildup.
- Daily Cleaning: Wipe down surfaces and remove excess powder.
- Weekly Cleaning: Disassemble parts in contact with the powder. Clean these parts thoroughly.
- Monthly Cleaning: Perform deep cleaning. Check for any dust in hard-to-reach areas.
Automatic Filling Machines often have sensitive sensors. Clean these carefully to ensure proper operation. A clean machine improves product quality and reduces contamination risks.
2. Inspect and Replace Worn Parts
Parts wear out over time. Inspecting and replacing these ensures the Powder Filling Machine continues running efficiently.
- Seals and Gaskets: Check for wear, as powder can leak through damaged seals.
- Nozzles and Funnels: Examine for clogs or damage. Powder buildup here disrupts flow.
- Sensors and Controls: Ensure sensors respond accurately. Faulty sensors can stop production.
Using original parts improves performance. Regular inspection helps avoid breakdowns and keeps the Automatic Filling Machine efficient.
3. Lubricate Moving Parts
Lubrication is essential for smooth operation. Without it, friction increases wear on parts, reducing machine life.
- Gears and Bearings: Apply recommended lubricants regularly. Follow manufacturer guidelines.
- Feed Mechanism: Lubricate to prevent powder buildup that can clog parts.
- Conveyor and Belt Systems: Regular lubrication prevents jamming and ensures a steady powder flow.
Avoid over-lubricating, as excess oil attracts dust. Consistent lubrication maintains the machine’s performance.
4. Calibrate for Accuracy
Calibrating the Powder Filling Machine is vital for accurate filling. Regular calibration reduces product waste and ensures consistency.
- Scale Calibration: Check weight accuracy. Inaccurate scales result in underfilled or overfilled products.
- Flow Rate Adjustment: Set the correct flow rate for different powders. Adjust based on powder density.
- Sensor Calibration: Ensure sensors are detecting correctly. This prevents accidental stoppages.
An Automatic Filling Machine with precise calibration produces higher-quality products. Regular calibration reduces product waste and maximizes production efficiency.
5. Train Operators
Skilled operators reduce the risk of machine damage. Proper training ensures the Powder Filling Machine operates smoothly.
- Basic Operation: Teach staff correct operating steps to prevent damage.
- Troubleshooting Skills: Train operators to recognize minor issues before they escalate.
- Maintenance Knowledge: Ensure operators understand basic maintenance steps.
Trained operators can quickly spot problems, preventing machine breakdowns. Well-informed staff improves productivity and maintains machine health.
6. Schedule Preventive Maintenance
Preventive maintenance reduces breakdowns. It’s essential for the Automatic Filling Machine to receive timely inspections.
- Weekly Checkups: Inspect belts, seals, and nozzles for wear.
- Monthly Checkups: Clean sensors, recalibrate the machine, and tighten loose parts.
- Annual Checkups: Perform a comprehensive check with a professional technician.
Preventive maintenance ensures continuous production. It helps reduce downtime and extends machine life.
7. Monitor Software and Controls
Modern Automatic Filling Machines use software for control. Monitoring and updating the software improves performance.
- Software Updates: Check for updates to improve functionality and security.
- Control Calibration: Ensure that all controls are responsive. This prevents filling errors.
- Error Logs: Review error logs regularly. This helps identify patterns that could signal a problem.
Software maintenance keeps the machine up-to-date and efficient. Updated controls reduce operational errors, enhancing productivity.
8. Store Powders Properly
Improper storage affects the Powder Filling Machine’s efficiency. Powders absorb moisture, leading to clogs or malfunctions.
- Dry Storage: Store powders in a dry environment to prevent clumping.
- Temperature Control: Keep powders at the right temperature to maintain flow.
- Sealed Containers: Use sealed containers to keep powders free from contaminants.
Well-stored powders improve machine performance. They reduce the risk of blockages and protect machine components.
9. Test for Consistent Powder Flow
Powder flow affects machine accuracy. Testing flow rates ensures consistent product filling.
- Flow Rate Testing: Adjust settings for different powders. Finer powders may require lower speeds.
- Clog Prevention: Check for buildup in nozzles. Clear any clogs before restarting.
- Discharge System Testing: Make sure discharge is smooth. Adjust settings to prevent overflow.
Consistent flow ensures the Automatic Filling Machine fills correctly. Testing reduces interruptions and maintains quality.
10. Check Safety Features
Safety features protect both the machine and the operators. Regular checks prevent accidents.
- Emergency Stop: Ensure it functions properly.
- Safety Guards: Check for secure attachment and no damage.
- Alarm Systems: Verify alarms work correctly to detect issues early.
A safe machine is a productive machine. Reliable safety features reduce the risk of accidents and prevent costly repairs.
11. Use Quality Spare Parts
Quality parts are essential for the Powder Filling Machine. They improve performance and ensure durability.
- Original Parts: Use parts recommended by the manufacturer.
- High-Quality Lubricants: Proper lubrication keeps the machine running smoothly.
- Certified Components: Only use certified components for replacements.
Quality spare parts reduce maintenance needs. They improve the machine’s lifespan and efficiency.
12. Maintain a Clean Environment
A clean workspace reduces the risk of contamination and equipment failure. Dust and dirt can damage sensitive parts in the Automatic Filling Machine.
- Clean Floors and Surfaces: Keep the area free from dust.
- Control Humidity: Use dehumidifiers to keep the air dry.
- Separate Work Zones: Designate areas for powder handling and equipment.
A clean environment ensures machine health. It improves filling accuracy and reduces downtime.
Conclusion: Maximizing Machine Longevity
Maintaining a Powder Filling Machine requires regular care and attention. Proper maintenance, cleaning, and inspection prevent breakdowns. Using quality parts and keeping the environment clean extends machine life. When combined with trained operators and preventive maintenance, these steps ensure your machine runs efficiently.
By following these practices, your Automatic Filling Machine will have fewer interruptions. It will maintain consistent quality and contribute to a smoother production line. Invest in maintenance today for a machine that works efficiently for years to come.