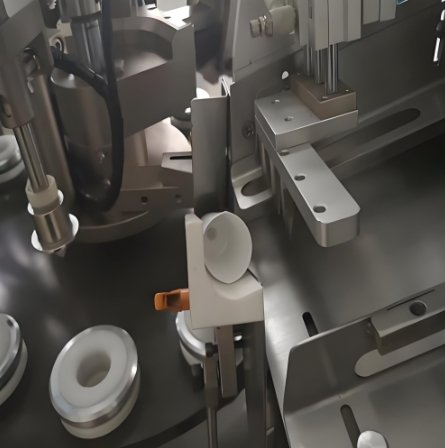
A Tube Filling and Sealing Machine is essential for production. It ensures accurate filling and perfect sealing. An Automatic Filling Machine improves speed and consistency. But mistakes can cause problems. Avoiding these errors improves efficiency.
Let’s look at the top mistakes and how to prevent them.
1. Using the Wrong Tube Material
A Tube Filling and Sealing Machine works with different tube materials. Some require heat sealing. Others need mechanical sealing.
Common Mistakes:
- Using heat sealing on aluminum tubes.
- Applying too much pressure on plastic tubes.
- Selecting weak materials that break easily.
How to Avoid It:
- Match the tube material with the sealing method.
- Adjust machine settings based on material type.
- Test samples before full production.
An Automatic Filling Machine runs smoothly when using the right tubes.
2. Incorrect Filling Volume
A Tube Filling and Sealing Machine must dispense the right amount. Overfilling wastes product. Underfilling leads to rejection.
Common Mistakes:
- Setting incorrect volume measurements.
- Ignoring viscosity differences.
- Not calibrating the machine.
How to Avoid It:
- Set precise fill levels before production.
- Adjust for different product viscosities.
- Perform regular calibration.
An Automatic Filling Machine should fill consistently to avoid waste.
3. Poor Sealing Quality
A Tube Filling and Sealing Machine must create strong seals. Weak seals cause leakage.
Common Mistakes:
- Incorrect sealing temperature.
- Too much or too little pressure.
- Dirty sealing bars.
How to Avoid It:
- Set the right temperature for each material.
- Apply consistent sealing pressure.
- Clean sealing bars regularly.
An Automatic Filling Machine ensures perfect seals when maintained properly.
4. Inconsistent Tube Positioning
A Tube Filling and Sealing Machine must align tubes perfectly. Misalignment affects sealing.
Common Mistakes:
- Improper tube loading.
- Misaligned nozzles.
- Loose tube holders.
How to Avoid It:
- Load tubes correctly every time.
- Adjust nozzle positions for accuracy.
- Tighten tube holders to prevent movement.
An Automatic Filling Machine ensures uniform placement for better results.
5. Lack of Regular Maintenance
A Tube Filling and Sealing Machine requires upkeep. Neglecting maintenance causes breakdowns.
Common Mistakes:
- Skipping routine cleaning.
- Not lubricating moving parts.
- Ignoring wear and tear.
How to Avoid It:
- Clean the machine after every shift.
- Lubricate moving components regularly.
- Inspect parts and replace worn-out ones.
An Automatic Filling Machine runs longer with proper care.
6. Using Low-Quality Tubes
A Tube Filling and Sealing Machine works best with high-quality tubes. Poor materials cause defects.
Common Mistakes:
- Choosing weak or thin tubes.
- Ignoring supplier quality.
- Using tubes with inconsistent sizing.
How to Avoid It:
- Use strong, durable tube materials.
- Work with reliable suppliers.
- Check tube quality before production.
An Automatic Filling Machine performs best with high-quality tubes.
7. Incorrect Machine Settings
A Tube Filling and Sealing Machine has adjustable settings. Wrong settings lead to errors.
Common Mistakes:
- Incorrect speed settings.
- Wrong pressure adjustments.
- Using default settings for all products.
How to Avoid It:
- Adjust speed for different tube sizes.
- Set pressure based on material type.
- Customize settings for each product.
An Automatic Filling Machine must be programmed correctly for accuracy.
8. Ignoring Operator Training
A Tube Filling and Sealing Machine needs skilled operators. Poor training leads to mistakes.
Common Mistakes:
- Untrained staff handling machines.
- Not updating employees on machine features.
- Ignoring troubleshooting steps.
How to Avoid It:
- Train operators on machine functions.
- Provide refresher courses regularly.
- Teach troubleshooting for quick fixes.
An Automatic Filling Machine works best with knowledgeable operators.
9. Not Monitoring Output Quality
A Tube Filling and Sealing Machine should produce high-quality tubes. Without checks, defects increase.
Common Mistakes:
- Skipping quality inspections.
- Not checking for leaks or poor seals.
- Ignoring slight variations in filling levels.
How to Avoid It:
- Inspect tubes after filling and sealing.
- Check for leaks and weak seals.
- Measure fill levels to ensure accuracy.
An Automatic Filling Machine ensures quality with regular inspections.
10. Overlooking Safety Measures
A Tube Filling and Sealing Machine has moving parts. Ignoring safety is dangerous.
Common Mistakes:
- Not wearing protective gear.
- Skipping machine safety checks.
- Allowing unauthorized personnel to operate it.
How to Avoid It:
- Require protective gear for all operators.
- Perform daily safety inspections.
- Restrict machine access to trained staff.
An Automatic Filling Machine operates safely with proper precautions.
A Tube Filling and Sealing Machine improves production. But common mistakes lead to problems. An Automatic Filling Machine runs efficiently with proper maintenance and correct settings.
Avoid these mistakes to maximize efficiency. Proper training, quality control, and machine care ensure the best results!