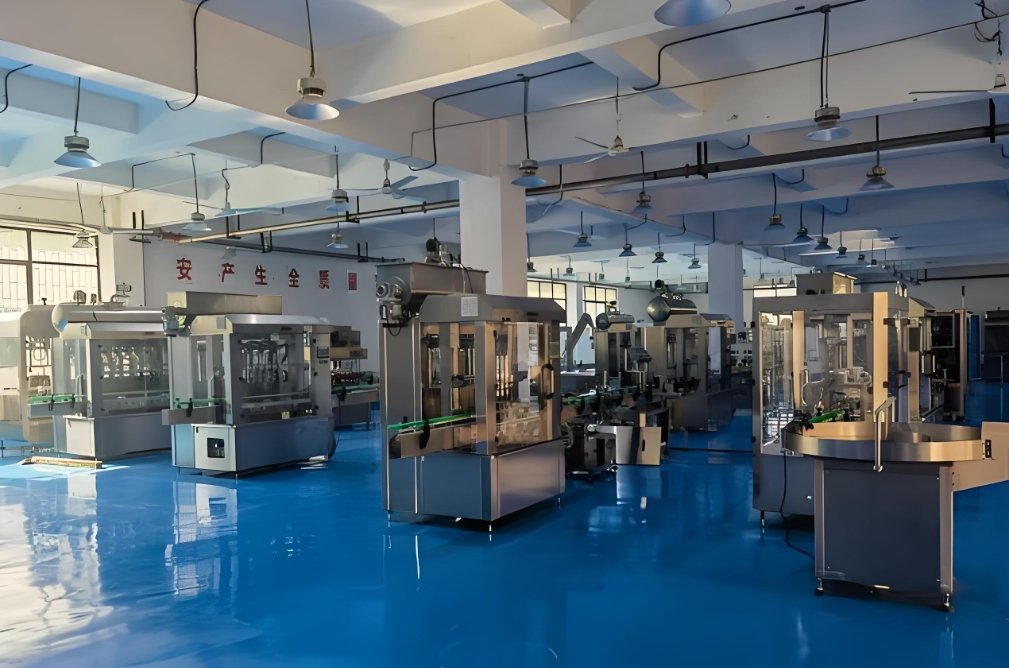
The Role of Filling Machines in a Fully Automated Facility
In a fully automated facility, efficiency is key. Filling machines are essential components of this efficiency. They ensure that products are filled accurately and quickly. An automatic filling machine can significantly enhance production processes.
This article explores the role of filling machines in fully automated environments. We will discuss their benefits, types, and how they integrate into production lines.
What is a Filling Machine?
A filling machine is designed to fill containers with products. These products can be liquids, powders, or pastes. Filling machines vary in design based on the product type and packaging requirements. An automatic filling machine operates without manual intervention. This automation improves speed and accuracy.
Filling machines are used across many industries. This includes food and beverage, pharmaceuticals, cosmetics, and chemicals. In a fully automated facility, these machines work seamlessly with other equipment.
Benefits of Filling Machines in Automation
Filling machines offer numerous advantages in a fully automated facility:
1. Increased Efficiency
Filling machines are faster than manual filling methods. They can fill hundreds of containers per minute. This speed increases overall production efficiency. An automatic filling machine reduces the time needed for filling processes.
2. Consistent Accuracy
Automatic filling machines provide consistent fill levels. This accuracy is crucial for maintaining quality control. It minimizes waste and ensures that each container meets specifications.
3. Reduced Labor Costs
With an automatic filling machine, fewer workers are needed. This reduces labor costs. The workforce can focus on other important tasks, improving overall productivity.
4. Scalability
Filling machines can easily adapt to changing production needs. As demand increases, facilities can scale up operations without major adjustments. This flexibility is vital in a dynamic market.
5. Improved Safety
Automatic filling machines reduce the risk of accidents. They minimize human interaction with hazardous materials. This increases workplace safety for employees.
Types of Filling Machines
Different types of filling machines serve various applications in automated facilities:
1. Liquid Filling Machines
Liquid filling machines handle products like water, juices, and oils. These machines can be gravity, piston, or pump-based. They ensure fast and accurate filling for liquid products.
2. Powder Filling Machines
Powder filling machines are used for dry products, such as flour and coffee. These machines often use auger systems to measure and fill powders accurately.
3. Paste Filling Machines
Paste filling machines handle thicker products like sauces and creams. These machines use piston systems to dispense viscous materials effectively.
4. Granular Filling Machines
Granular filling machines are designed for products like rice and nuts. They fill containers with granulated materials accurately and efficiently.
Each type of machine plays a vital role in the overall automation process.
Integration of Filling Machines in Automated Facilities
Filling machines are integrated into a larger automated system. This system includes various components such as conveyors, labelers, and packaging machines. The integration enhances the overall workflow.
1. Conveyor Systems
Conveyor systems transport products to and from filling machines. This automation reduces manual handling and increases efficiency. The filling machine can operate seamlessly with the conveyor, ensuring a smooth production flow.
2. Labeling and Capping Machines
After filling, products need to be labeled and capped. Automatic filling machines can connect directly with labeling and capping machines. This integration streamlines the entire packaging process.
3. Quality Control Systems
Quality control is crucial in a fully automated facility. Filling machines can be equipped with sensors to monitor fill levels. These sensors provide real-time data, ensuring that each product meets quality standards.
4. Data Management Systems
Automated facilities use data management systems to track production metrics. Filling machines can integrate with these systems to provide data on fill accuracy and speed. This data helps optimize operations and improve decision-making.
Best Practices for Using Filling Machines
To maximize the benefits of filling machines in an automated facility, consider these best practices:
1. Regular Maintenance
Routine maintenance is essential for keeping filling machines in optimal condition. Schedule regular checks to identify and resolve issues before they lead to downtime.
2. Employee Training
Train employees on how to operate filling machines. Proper training ensures that staff can troubleshoot minor issues and maintain safety standards.
3. Continuous Improvement
Monitor the performance of filling machines regularly. Analyze data to identify areas for improvement. This continuous improvement process can enhance efficiency and product quality.
4. Adapt to Market Changes
Stay informed about market trends and changes. Be ready to adapt filling machine operations to meet new demands. This flexibility will keep your facility competitive.
Filling machines play a critical role in fully automated facilities. They enhance efficiency, accuracy, and safety while reducing labor costs. With various types of filling machines available, businesses can choose the right solution for their specific needs.
Integrating filling machines with other automated systems creates a streamlined production line. Following best practices ensures optimal performance and productivity. Investing in an automatic filling machine is a smart choice for any business looking to improve its operations and maintain a competitive edge in today’s market.