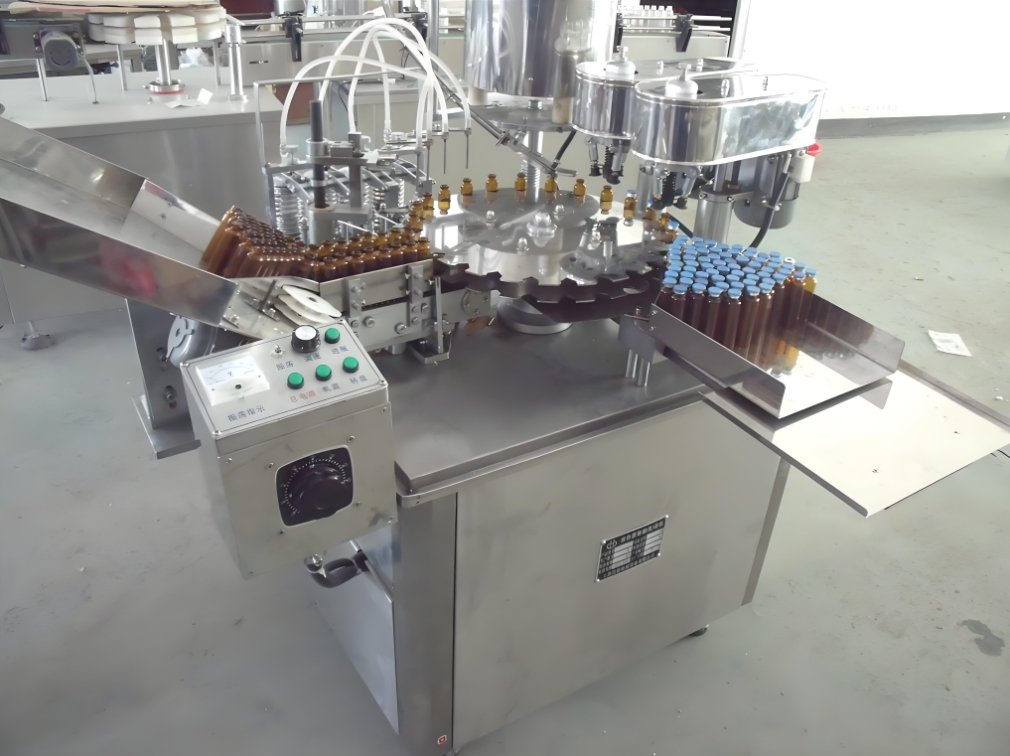
A filling machine is crucial for many industries. Whether it’s for packaging food, beverages, cosmetics, or chemicals, a reliable filling machine is a must. But like all machines, automatic filling machines can face wear and tear over time. If not maintained properly, they can break down and cause costly delays.
Being aware of the signs that your filling machine needs repairs can prevent breakdowns and extend its life.
1. Inconsistent Filling Volumes
One of the clearest signs of trouble is inconsistent filling volumes. If your machine suddenly starts overfilling or underfilling containers, something is wrong.
This could be due to:
- Worn-out nozzles
- Clogged valves
- Calibration issues
Fixing these issues quickly can prevent further problems. Recalibrate the machine, clean the nozzles, and inspect the valves regularly.
2. Frequent Downtime
If your automatic filling machine stops often during production, it’s a sign that repairs may be needed. Machines designed to run smoothly should not experience frequent downtime.
The causes of this can include:
- Electrical malfunctions
- Damaged moving parts
- Blockages in the system
If downtime becomes more frequent, inspect the machine immediately. Early intervention can prevent bigger repairs.
3. Leaks
Leaks around the nozzles, valves, or hoses can cause significant product waste. A well-functioning filling machine should not leak during operation.
Leaks may happen because of:
- Worn seals or gaskets
- Loose fittings
- Cracked hoses
Fixing leaks right away ensures product quality and prevents damage to the machine’s components.
4. Unusual Noises
Filling machines are usually quiet when operating properly. But when something goes wrong, you might hear unusual noises such as grinding, squeaking, or knocking sounds.
These noises can be caused by:
- Loose or worn-out parts
- Improper lubrication
- Motor issues
Ignoring strange sounds can lead to machine failure. Listen closely and take action if you notice any unfamiliar noises.
5. Decreased Speed or Efficiency
When your automatic filling machine slows down, it affects your production line. If it takes longer than usual to fill each container, something is not right.
A decrease in speed could be caused by:
- Clogged nozzles
- Poorly calibrated machine settings
- Worn or damaged parts
Sluggish performance leads to delays and lost productivity. Inspect your machine and address any issues to restore its efficiency.
6. Product Contamination
If you notice that products filled by the machine are contaminated, immediate repairs are required. Contamination can occur if the machine isn’t properly cleaned or if parts are malfunctioning.
Contamination issues might result from:
- Residue buildup inside the machine
- Leaks mixing different liquids
- Cracked or worn parts allowing contaminants in
Clean the machine thoroughly and replace any damaged parts to ensure that the product remains safe and uncontaminated.
7. Error Messages or Alarms
Most modern automatic filling machines have built-in error detection systems. If your machine starts displaying error messages or sounding alarms, it’s trying to alert you to an issue.
Common causes of error messages include:
- Overfilled containers
- Sensor malfunctions
- Blocked filling heads
Pay attention to these warnings. Diagnosing the problem as soon as possible can save you from more significant repairs.
8. Pressure Fluctuations
Pressure is important for proper filling. If your machine relies on air or hydraulic pressure, fluctuations in pressure can cause filling inconsistencies.
Pressure problems can stem from:
- Leaking hoses
- Faulty pumps
- Malfunctioning pressure regulators
Monitor pressure levels regularly. If you notice erratic pressure readings, it’s time to call for repairs.
9. Misaligned Nozzles
Nozzles are essential to accurate filling. If the nozzles are not properly aligned, the machine can spill product or miss containers entirely.
Misalignment may result from:
- Loose fittings
- Wear and tear on components
- Frequent adjustments without recalibration
Fixing nozzle alignment issues promptly ensures accurate filling and prevents product waste.
10. Electrical Issues
Electrical problems can cause your filling machine to malfunction. If the machine fails to power on, or if it keeps shutting down unexpectedly, it could be due to electrical faults.
Electrical problems might arise from:
- Faulty wiring
- Damaged circuits
- Malfunctioning sensors
Always check for loose or frayed wires. If electrical issues persist, professional repair may be needed.
When to Call a Professional
Minor issues like cleaning or recalibration can often be handled in-house. However, more complex problems, especially electrical or motor-related issues, require professional attention.
Signs you need professional repairs include:
- Persistent error messages
- Electrical problems that won’t resolve
- Continuous leaks or product contamination
Attempting to fix these issues without expert knowledge can lead to more damage. It’s best to rely on professionals for major repairs.
Extending the Life of Your Filling Machine
By recognizing these signs early and conducting regular maintenance, you can extend the life of your filling machine. Here are some key tips:
1. Clean Regularly
Always clean the machine after every production run. This prevents product residue from building up and ensures smooth operation.
2. Lubricate Moving Parts
Proper lubrication reduces friction and wear on moving parts. This keeps the machine running smoothly and extends its lifespan.
3. Inspect Parts Often
Check nozzles, seals, hoses, and valves regularly for wear and tear. Replace any damaged parts immediately to avoid breakdowns.
4. Calibrate Frequently
Recalibrate the machine regularly to ensure accurate filling volumes. This prevents inconsistent fills and maintains product quality.
5. Monitor Electrical Systems
Inspect the machine’s electrical components to ensure everything is working correctly. Loose connections or faulty sensors can lead to machine failures.
Conclusion
Maintaining your filling machine is essential for efficient production. By recognizing the warning signs of trouble—such as leaks, inconsistent filling, and strange noises—you can prevent costly breakdowns. Regular maintenance, including cleaning, lubricating, and inspecting parts, ensures that your automatic filling machine runs smoothly and lasts longer.
Don’t ignore the signs that your machine needs repairs. Taking action early can save time, money, and headaches in the long run.
very good