Types of Sealing in Tuble Filling Machines
In the packaging industry, the tuble filling machine plays a crucial role in efficiently filling and sealing products into tubes. These machines are indispensable in various sectors, including cosmetics, food, and pharmaceuticals. They ensure that products are filled accurately and sealed securely, preserving their quality and extending their shelf life. This article will delve deeper into the applications of tuble filling machines, the different sealing methods used, and the benefits of each.
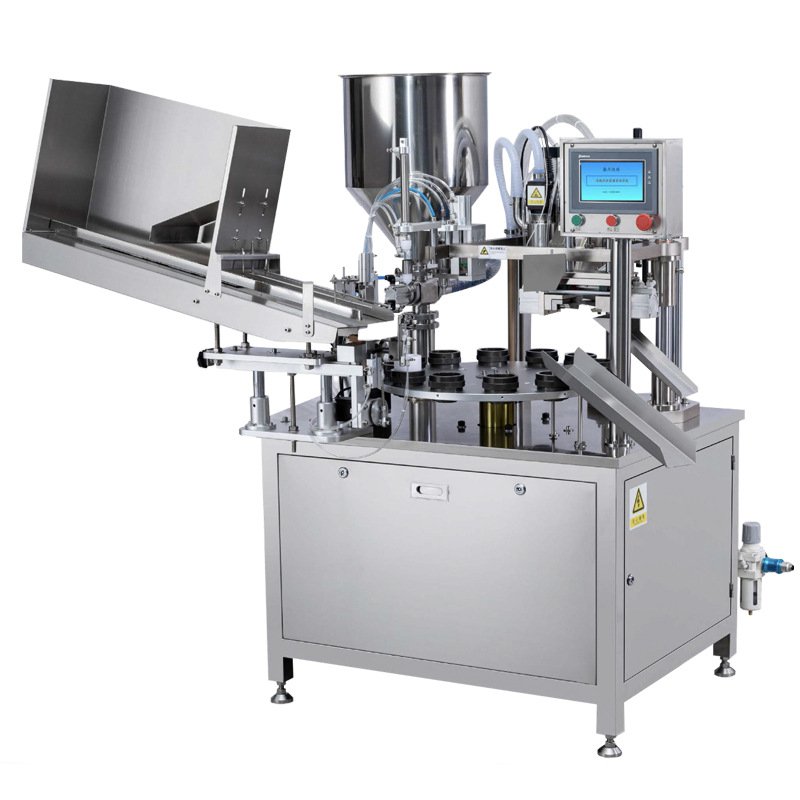
Applications of Tuble Filling Machines
Tuble filling machines are versatile and can accommodate a wide range of products. Here are some of the most common applications:
Cosmetics: Tuble filling machines are widely used for packaging products like creams, lotions, gels, and toothpaste. In the cosmetics industry, maintaining product integrity and presentation is vital. A tuble filling machine ensures precise filling without spills, helping to keep the packaging clean and professional.
Food Products: Various food products, including sauces, pastes, and dressings, are frequently packaged in tubes. These machines help maintain hygiene and prevent contamination, which is crucial for food safety. For instance, mayonnaise or mustard can be filled into tubes, allowing consumers to dispense just the right amount without the risk of cross-contamination.
Pharmaceuticals: Tuble filling machines are essential for packaging ointments, gels, and other medicinal products. The accurate filling and sealing provided by these machines are critical for maintaining the effectiveness and safety of medications. In this sector, where precision is paramount, a tuble filling machine helps ensure that each product meets regulatory standards.
Industrial Applications: Beyond consumer goods, tubes are also used for packaging adhesives, sealants, and lubricants. Tuble filling machines ensure that these industrial products are filled and sealed for optimal performance. In industries where quality control is essential, these machines play a vital role in maintaining consistency and reliability.
Types of Sealing in Tuble Filling Machines
Sealing is a critical step in the tuble filling process. The two most common sealing methods used in these machines are heat sealing and ultrasonic sealing. Each method has its unique advantages and applications, making it essential for manufacturers to choose wisely based on their needs.
Heat Sealing
Heat sealing is a widely used method in tuble filling machines. This process involves applying heat to the end of the tube, causing the material to soften and bond together. Key points about heat sealing include:
Temperature Control: Heat sealing machines allow for precise temperature control, ensuring that the seal is strong and reliable. Maintaining the right temperature is crucial to preventing leaks and maintaining product freshness. If the temperature is too low, the seal may not form properly, leading to product spoilage.
Material Compatibility: This method is effective with various tube materials, including plastic and aluminum. It is suitable for many applications, particularly in cosmetics and food packaging. Manufacturers can select the appropriate material for their products, ensuring compatibility with the heat sealing process.
Cost-Effectiveness: Heat sealing machines are generally more affordable and easier to maintain than ultrasonic sealing machines. This makes them a popular choice for many manufacturers, especially those with tighter budgets. Additionally, the simplicity of heat sealing technology can lead to lower operational costs in the long run.
Ease of Operation: Heat sealing processes are relatively straightforward, allowing operators to become proficient quickly. This ease of use can lead to faster training times and lower labor costs.
Ultrasonic Sealing
Ultrasonic sealing is a newer technology that utilizes high-frequency sound waves to create a seal. This method offers several advantages:
Fast and Efficient: Ultrasonic sealing is quicker than heat sealing. The sealing process can occur almost instantaneously, increasing production speed and efficiency. This speed is especially beneficial for high-volume production lines, where time is a critical factor.
Strong Seals: Seals created using ultrasonic technology are often stronger and more reliable. This is particularly important for products requiring long shelf lives or sensitive contents. The durability of the seals helps prevent leakage and ensures that products remain intact during transportation and storage.
Lower Temperature: Ultrasonic sealing operates at lower temperatures compared to heat sealing. This reduces the risk of damaging heat-sensitive products. For example, many cosmetics contain ingredients that can be altered by high temperatures, making ultrasonic sealing an ideal choice for preserving product integrity.
Reduced Energy Consumption: Ultrasonic sealing technology typically consumes less energy than traditional heat sealing methods. This can lead to lower operational costs and a smaller carbon footprint, appealing to environmentally conscious manufacturers.
Choosing the Right Sealing Method
The choice between heat sealing and ultrasonic sealing depends on several factors, including the type of product, packaging material, and production volume. Here are some considerations for manufacturers:
Product Sensitivity: If the product is sensitive to heat, ultrasonic sealing may be the better choice. It protects the product while still providing a strong seal, ensuring that quality is maintained throughout the packaging process.
Production Speed: For high-volume production lines, ultrasonic sealing offers speed advantages that can enhance overall efficiency. Faster sealing times lead to quicker turnaround and improved productivity.
Cost and Budget: While heat sealing machines tend to be more cost-effective upfront, manufacturers should consider long-term operational costs and maintenance when making a decision. Ultrasonic sealing machines may require a larger initial investment, but their efficiency and energy savings can pay off over time.
The tuble filling machine is a vital component in packaging various products across multiple industries. Whether in cosmetics, food, pharmaceuticals, or industrial applications, these machines ensure accurate filling and secure sealing. By understanding the different sealing methods—heat sealing and ultrasonic sealing—manufacturers can choose the right technology for their specific needs.
Investing in a reliable tuble filling machine equipped with the appropriate sealing method can lead to enhanced product quality, improved efficiency, and increased customer satisfaction. For businesses aiming to optimize their packaging processes, the right choice in machinery can make a significant difference in overall success. With the right equipment, manufacturers can streamline their operations, reduce waste, and deliver high-quality products to their customers.