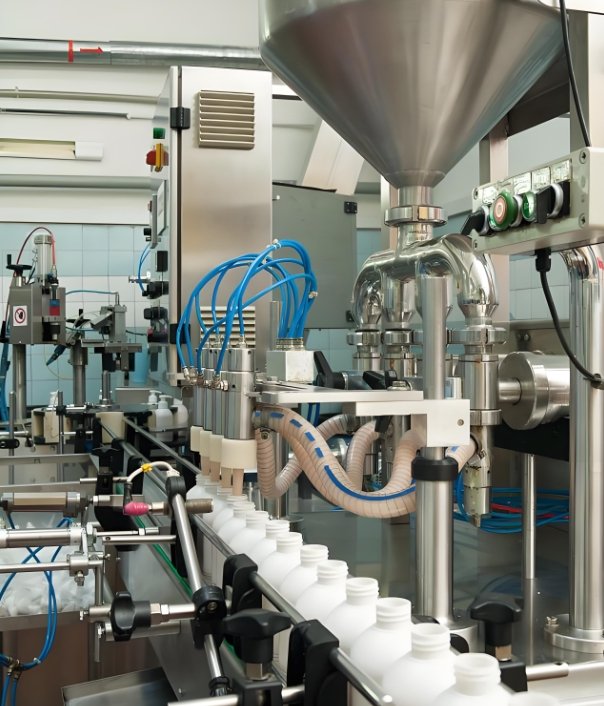
Filling machines play a crucial role in the industrial chemical sector. These machines ensure that containers are filled accurately and safely. When working with industrial chemicals, choosing the right filling machine is vital for efficiency and quality control. This article explores important considerations when selecting and using filling machines for industrial chemicals, including automatic filling machines.
1. Importance of Filling Machines in the Industrial Chemical Industry
Filling machines are essential in industries that deal with chemicals. Chemicals often need precise filling to avoid overflows or underfilling. Filling machines provide consistent filling volumes, improving accuracy. They also reduce the risks of handling hazardous materials.
Automatic filling machines take this a step further by automating the process. Automation minimizes human contact with harmful substances. It also increases production speed. For large-scale operations, these machines are crucial.
2. Types of Filling Machines Used for Chemicals
There are various types of filling machines suited for chemicals. The type of machine depends on the nature of the chemical being filled.
a. Liquid Filling Machines
Liquid filling machines are commonly used for thin or semi-viscous chemicals. They ensure precise filling for liquids such as solvents and oils.
b. Viscous Liquid Filling Machines
These machines handle thick liquids like adhesives or gels. Automatic filling machines designed for viscous chemicals use pumps to ensure the right amount is filled.
c. Powder Filling Machines
Powder filling machines are used for powdered chemicals like cleaning agents. These machines carefully measure the product before dispensing it into containers.
Each type of filling machine is designed to handle specific chemical properties. It is essential to select the machine that best matches the chemical’s state—whether it is a liquid, powder, or viscous material.
3. Key Considerations When Choosing a Filling Machine
Choosing the right filling machine for industrial chemicals requires careful thought. There are several factors to consider:
a. Chemical Compatibility
The filling machine should be compatible with the chemical being filled. Some chemicals are corrosive and require machines made from special materials like stainless steel or chemical-resistant plastic.
b. Production Volume
Consider the scale of production. For high-volume production, automatic filling machines are ideal. They fill containers faster than manual machines, boosting overall efficiency.
c. Viscosity and Chemical Properties
Different chemicals have different viscosities. A machine designed for liquid chemicals might not work for thicker substances. For viscous chemicals, a piston or pump filling machine may be needed.
d. Type of Containers
The machine must be able to handle the container size and shape used in your production. Some filling machines are designed for standard bottles, while others can handle a range of container types.
4. Benefits of Using Automatic Filling Machines for Industrial Chemicals
Automatic filling machines offer many benefits in the chemical industry. They streamline the filling process and enhance safety.
a. Increased Efficiency
An automatic filling machine can fill hundreds or even thousands of containers in a short period. This improves production efficiency, especially in large-scale operations.
b. Improved Accuracy
Automation ensures precise measurement for each container. This reduces waste, which is especially important when working with expensive chemicals.
c. Enhanced Safety
Many industrial chemicals are hazardous. Automatic filling machines reduce the need for workers to interact directly with dangerous chemicals. This minimizes the risk of accidents.
5. Challenges in Filling Industrial Chemicals
Despite their benefits, filling machines also come with challenges. Addressing these issues is important to keep operations running smoothly.
a. Maintenance Needs
Filling machines require regular maintenance. Chemicals can corrode machine parts over time. Regular cleaning and inspection are necessary to prevent breakdowns.
b. Initial Cost
Investing in automatic filling machines can be expensive upfront. However, the long-term savings in labor and efficiency often justify the investment.
c. Training Requirements
Proper training is essential for operating filling machines. Workers must understand how to use the machine and handle chemicals safely.
6. Safety Considerations for Filling Machines and Chemicals
Safety is a priority in the industrial chemical sector. Filling machines must meet safety standards to ensure the well-being of workers and the environment.
a. Protective Materials
The materials used in the filling machine should be resistant to the chemicals being handled. Stainless steel is a common choice due to its resistance to corrosion.
b. Explosion-Proof Design
Certain chemicals are flammable or explosive. In these cases, the machine must be designed to operate safely in hazardous environments.
c. Safety Features
Automatic filling machines often come equipped with safety features. These include emergency shutoff systems, alarms, and protective shields. Such features protect workers from chemical exposure.
7. Automation and Its Role in Industrial Chemical Filling
Automation plays a significant role in the chemical filling process. Automatic filling machines can run continuously, reducing downtime. They also integrate with other automated systems for a more efficient production line.
One advantage of automation is the ability to program machines for different container sizes. This flexibility allows companies to switch between products quickly. Automated systems can also monitor production in real-time, ensuring consistent quality.
8. Maintenance Tips for Filling Machines
Proper maintenance is essential to keep filling machines running smoothly. Here are some tips:
a. Regular Cleaning
Chemicals can leave residue inside machines. Clean the machine regularly to prevent clogs and corrosion.
b. Check for Wear and Tear
Inspect machine parts regularly. Replace worn-out parts before they cause bigger problems.
c. Lubrication
Keep moving parts lubricated to avoid unnecessary wear. This extends the machine’s lifespan and keeps it running efficiently.
d. Follow Manufacturer Guidelines
Always follow the manufacturer’s maintenance recommendations. They provide specific guidelines for cleaning, lubrication, and part replacement.
9. Future Trends in Filling Machines for Industrial Chemicals
The future of filling machines includes technological advancements that will improve efficiency and safety even further.
a. Smart Machines
Filling machines are becoming smarter, with sensors and AI technology. These machines can detect issues and make real-time adjustments for better accuracy.
b. Sustainability
As industries move toward greener practices, filling machines will adapt to handle eco-friendly packaging materials. This trend will likely include machines that use less energy and generate less waste.
c. Robotic Integration
In the future, filling machines may integrate more with robotic systems. This will further reduce the need for manual labor and improve overall productivity.
Choosing the right filling machine for industrial chemicals is crucial for safety, efficiency, and cost-effectiveness. Automatic filling machines provide numerous advantages, from increased production speed to enhanced safety measures. Understanding the key considerations—such as chemical properties, container types, and machine materials—ensures that your operations run smoothly. While challenges like maintenance and training exist, the benefits of using filling machines far outweigh the drawbacks. With advancements in automation and technology, the future of filling machines promises even greater innovation and efficiency in the industrial chemical sector.