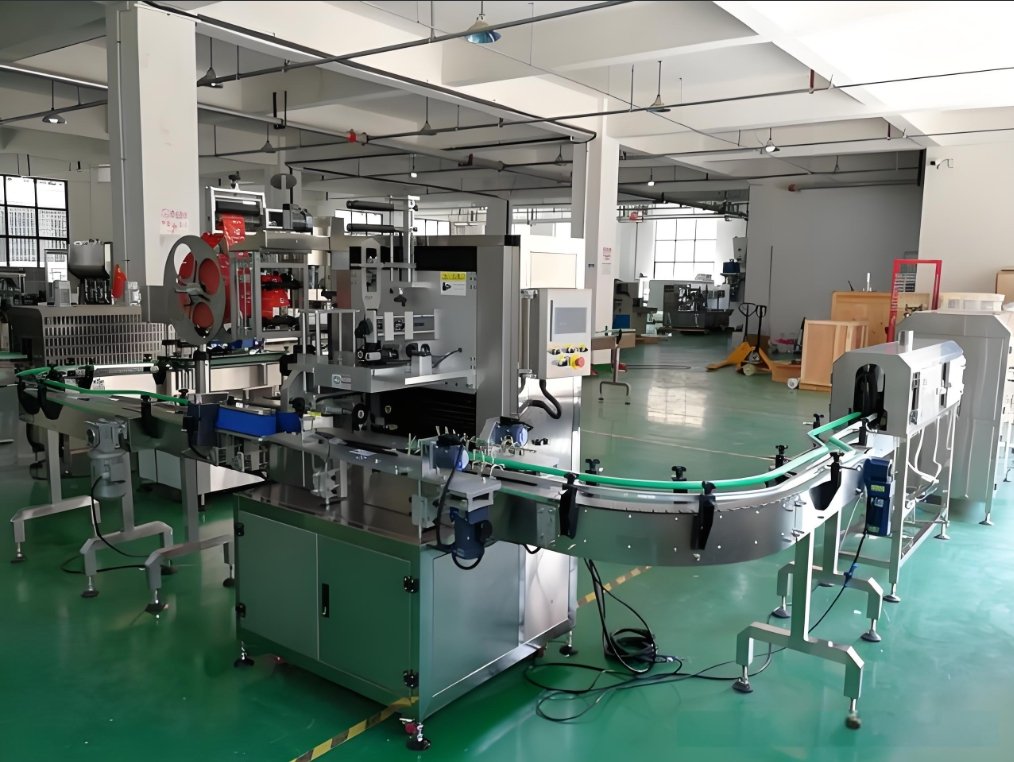
Filling machines play an essential role in manufacturing. Understanding customer feedback can help companies improve performance and efficiency. Automatic filling machines, in particular, need to meet user expectations. Customer feedback provides direct insights into what works and what doesn’t.
Why Customer Feedback is Important
Feedback is a valuable tool. It helps manufacturers understand their products better. Feedback on filling machines can lead to improvements in speed, accuracy, and reliability. Listening to customers helps companies stay competitive. An automatic filling machine that meets user needs gains more positive reviews. Satisfied customers bring more business through referrals.
Key Areas of Feedback on Filling Machines
Customer feedback usually centers on a few critical areas. Knowing these can help improve design and performance.
- Ease of UseCustomers want easy-to-operate filling machines. Complicated setups slow down production. Simple controls are highly valued. Users look for intuitive interfaces in automatic filling machines. A user-friendly design boosts satisfaction. It also reduces training time.
- Speed and EfficiencySpeed is a top priority in fast-paced industries. Customers want filling machines that keep up with demand. An automatic filling machine must be efficient. High-speed options save time. They also reduce production costs. Efficiency affects customer satisfaction directly. Faster machines mean quicker turnaround times.
- Accuracy and PrecisionPrecision is essential for consistent quality. Customers expect filling machines to measure accurately. Automatic filling machines should provide consistent results. Accurate measurements prevent product waste. They also help maintain quality standards.
- Durability and Reliability Filling machines must be reliable. Downtime disrupts production and affects profits. Customers prefer machines that last. Automatic filling machines should handle long production hours. Reliability is a significant factor in customer satisfaction. Machines that break down often get negative feedback.
- Maintenance RequirementsMaintenance is inevitable for any machine. However, customers prefer filling machines with minimal maintenance. Simple, quick maintenance tasks are preferred. Automatic filling machines should have easy-to-clean parts. Machines that are easy to maintain receive positive feedback.
- Safety FeaturesSafety is a crucial concern in manufacturing. Customers want filling machines with strong safety features. Automatic filling machines should have safeguards to protect operators. Safety measures increase trust in the machine. Safe machines receive better feedback.
- Customization OptionsEvery production line is unique. Customers value filling machines that offer customization. Automatic filling machines should be adaptable. Customizable options allow companies to meet specific needs. This flexibility is often a top feature in positive reviews.
Collecting Customer Feedback Effectively
Gathering feedback is only useful if done right. Effective feedback collection helps identify areas for improvement.
- Surveys and QuestionnairesSurveys are easy ways to gather customer opinions. Ask specific questions about filling machine performance. For automatic filling machines, focus on speed and efficiency. Surveys provide structured data that is easy to analyze.
- Product ReviewsReviews often highlight key strengths and weaknesses. Pay attention to recurring comments. Positive reviews can reveal which features matter most. Negative reviews point out areas for improvement. Encourage customers to leave reviews after purchase.
- Customer Service InteractionsCustomer support interactions provide direct feedback. Track common issues and questions. Customers often report problems first to support teams. Analyzing these interactions can reveal patterns. It also shows what frustrates users about filling machines.
- On-Site Visits and Demos Observing filling machines in use gives valuable insights. See how customers interact with automatic filling machines. On-site visits reveal operational issues and customer preferences. Demos allow customers to give real-time feedback.
- Follow-Up EmailsSend follow-up emails post-purchase. Ask for feedback on the filling machine. Automatic filling machines benefit from early feedback. Follow-ups show customers that feedback matters. They also strengthen customer relationships.
Interpreting and Using Feedback
Collecting feedback is only part of the process. Companies need to analyze and act on feedback effectively.
- Identify Common ThemesLook for recurring feedback themes. If multiple customers mention maintenance issues, it’s likely a problem. Common themes provide a clear direction for improvements.
- Prioritize Areas for ImprovementNot all feedback will be equally important. Prioritize changes that affect performance. Focus on areas like accuracy, speed, and ease of use. For automatic filling machines, prioritize reliability improvements.
- Implement Design AdjustmentsUse feedback to inform design changes. If customers want simpler controls, adjust the interface. Design changes based on feedback improve customer satisfaction.
- Regularly Update Products Regular updates keep filling machines competitive. Updating based on feedback shows customers their opinions matter. Frequent updates improve the overall product quality.
Benefits of Using Customer Feedback
Using customer feedback has several advantages. It improves product quality, customer satisfaction, and sales.
- Enhanced Product PerformanceFeedback-based improvements make filling machines better. Improved speed and accuracy lead to higher customer satisfaction.
- Increased Customer LoyaltySatisfied customers are loyal. Listening to feedback builds trust. Customers are more likely to recommend a filling machine they feel has improved based on their input.
- Reduced Negative ReviewsAddressing issues reduces complaints. Customer feedback helps companies identify and solve problems. Fewer complaints mean a better brand reputation.
- Product DifferentiationCustomer-driven improvements make filling machines stand out. Unique features based on feedback attract new customers. Differentiation helps companies gain a competitive edge.
Key Improvements Based on Feedback
Customers often suggest valuable changes. Incorporating these suggestions strengthens product offerings.
- Enhanced AutomationCustomers want more automation features. Upgraded automation options improve the filling machine’s efficiency. Automation also reduces manual errors.
- Improved Cleaning ProcessesCleaning can be time-consuming. Customers suggest easier cleaning mechanisms. Machines with detachable parts or self-cleaning features receive better feedback.
- User Interface UpgradesSimple, intuitive interfaces receive positive reviews. Upgrading the interface based on feedback improves user experience. This adjustment also reduces training time.
- Safety EnhancementsSafety is often a common feedback point. Adding extra safety features builds customer trust. Machines with strong safety measures gain more positive feedback.
- Energy EfficiencyCustomers prefer eco-friendly filling machines. Improved energy efficiency appeals to environmentally conscious buyers. Efficiency upgrades often result in positive reviews.
Customer feedback is essential for filling machine improvement. By understanding and acting on feedback, companies create better products. Positive feedback on automatic filling machines drives sales and brand loyalty. Continuous improvements based on feedback ensure filling machines meet industry needs. Using feedback effectively allows filling machines to become valuable assets in any production line. marketing positions the filling machine as a vital tool in packaging and production.