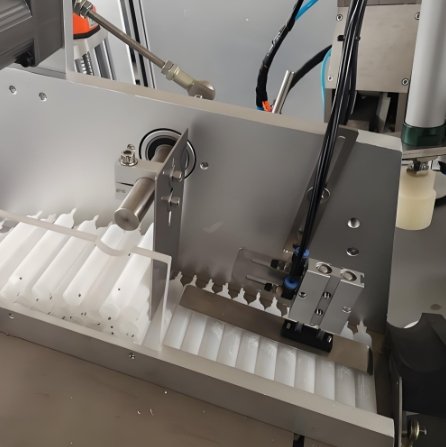
A Tube Filling and Sealing Machine is vital in many industries. It handles the filling and sealing of tubes with speed and accuracy. These machines make processes more efficient by reducing manual work. Understanding how they work helps businesses use them effectively.
This guide explains the step-by-step process. We’ll explore how the Automatic Filling Machine simplifies operations and ensures consistent results.
1. Introduction to Tube Filling and Sealing Machines
A Tube Filling and Sealing Machine automates the filling and sealing of tubes. It is widely used in industries like cosmetics, food, and pharmaceuticals. These machines are designed for both thin and thick liquids.
An Automatic Filling Machine offers high efficiency. It replaces manual labor and improves production speed. Understanding its operation ensures proper usage.
2. Tube Feeding Stage
The first step is feeding the tubes into the machine. This process is automatic. The operator loads a stack of empty tubes into the feeding system.
The machine places the tubes into designated holders. Each tube aligns perfectly. This ensures smooth processing.
3. Tube Orientation
Once the tubes are fed, they are oriented. Orientation ensures the tubes face the correct direction. This step is critical for consistent filling and sealing.
Sensors detect the tube’s position. If a tube is misaligned, the machine adjusts it automatically. Proper orientation prevents errors during filling and sealing.
4. Filling Process
The Automatic Filling Machine begins filling the tubes with the product. The filling nozzle moves into position. The product is dispensed in precise amounts.
This step is adjustable. The machine can fill tubes with liquids, creams, or pastes. For thicker products, a piston filling system is often used. The machine ensures no product spillage or overfilling.
5. Heating the Tube
After filling, the machine heats the top of the tube. This prepares the tube for sealing. The heating system can use hot air or ultrasonic waves.
Hot air systems blow heated air onto the tube’s edges. This softens the material. Ultrasonic systems use vibrations to generate heat. Both methods ensure the tube is ready for sealing.
6. Sealing the Tube
The Tube Filling and Sealing Machine seals the tube. The softened edges are pressed together. The machine applies pressure to ensure a strong seal.
Sealing can be done in various styles. Some machines offer flat seals. Others provide round or custom-shaped seals. A strong seal prevents leaks and keeps the product secure.
7. Printing or Embossing
Some machines include a printing or embossing feature. After sealing, they mark the tube with a code, date, or logo. This step is optional but important for branding or tracking.
The machine ensures the print is clear and positioned correctly. It happens quickly to avoid delays in production.
8. Trimming the Tube
Once sealed, the machine trims any excess material. This creates a clean and polished look. Trimming ensures uniformity across all tubes.
A sharp blade removes extra material precisely. This step gives the product a professional appearance.
9. Discharging the Tube
The final step is discharging. The finished tubes are removed from the machine. They are placed onto a conveyor belt or into a collection bin.
The machine ensures all tubes are sealed and filled correctly before discharge. Faulty tubes are separated automatically.
10. Why Use an Automatic Filling Machine?
An Automatic Filling Machine offers many benefits. It saves time and reduces errors. Here’s why businesses prefer it:
- Speed: The machine fills and seals tubes quickly.
- Accuracy: Precise filling reduces waste.
- Consistency: Every tube looks the same.
- Efficiency: It handles high production volumes with ease.
Small and large businesses benefit from automation. It improves output and maintains quality.
11. Maintenance and Care
To keep the machine running smoothly, regular maintenance is essential. Clean the filling system daily. Check the sealing unit for wear and tear. Lubricate moving parts to prevent friction.
Inspect the sensors and heating system weekly. Proper care ensures the Tube Filling and Sealing Machine works efficiently.
12. Applications of Tube Filling and Sealing Machines
These machines are used in various industries:
- Cosmetics: For creams, gels, and lotions.
- Pharmaceuticals: For ointments and medicated gels.
- Food: For sauces, pastes, and edible gels.
- Chemicals: For adhesives and industrial products.
The Automatic Filling Machine is versatile. It handles different products and tube materials.
A Tube Filling and Sealing Machine simplifies production. It automates filling, sealing, and other steps with precision. Using an Automatic Filling Machine ensures consistent results and reduces errors.
Understanding how these machines work helps businesses maximize their potential. Regular maintenance keeps them running smoothly. Investing in a quality machine improves efficiency and product quality. Whether for cosmetics, food, or pharmaceuticals, these machines are a valuable asset.
Automate your tube filling process today for better results!