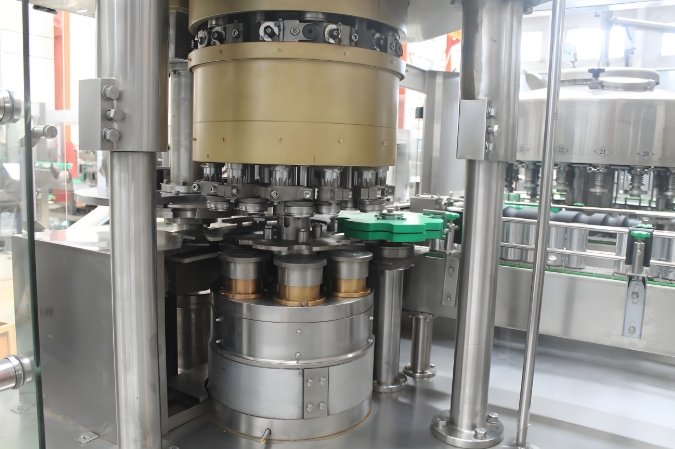
High-pressure beverages need special equipment. Beverage filling machines play a vital role. They ensure safety and efficiency. Advanced technology in these machines makes them reliable.
Why High-Pressure Beverages Require Special Handling
Drinks like soda and sparkling water are carbonated. They contain pressurized gas. Filling these requires precision. Without it, spillage and contamination occur. An automatic filling machine ensures consistent quality.
Features of a High-Pressure Beverage Filling Machine
- Pressure Control
High-pressure drinks need stable systems. Machines monitor and adjust pressure levels. - Leak-Proof Sealing
Carbonated drinks require tight seals. Advanced seals prevent gas loss. - Foam Reduction
Excess foam causes waste. Foam-control mechanisms reduce this problem. - Speed Adjustment
High-speed filling prevents delays. Machines adapt to various container types.
Advantages of an Automatic Filling Machine for Carbonated Drinks
- Consistency
Machines fill each bottle evenly. This prevents overfilling or underfilling. - Hygiene
Automatic systems reduce human contact. This ensures product safety. - Cost-Effectiveness
Automation reduces labor costs. It also minimizes material waste. - Versatility
Machines handle different bottle sizes. They also adjust to varying pressure needs.
Key Components of a High-Pressure Beverage Filling Machine
- Pressure Valves
These maintain steady gas levels. - Advanced Sensors
Sensors detect leaks or irregularities. - Durable Nozzles
Nozzles withstand high pressure. They also ensure precise filling. - Sealing Mechanisms
Secure caps lock in carbonation.
Applications of High-Pressure Automatic Filling Machines
- Soft Drink Bottling
These machines are ideal for soda production. They handle various bottle sizes with ease. - Sparkling Water Plants
Machines maintain gas levels. They also ensure fast production. - Alcoholic Beverages
Carbonated drinks like beer use these systems. Precise filling keeps flavor intact.
Common Problems with High-Pressure Filling
- Gas Loss
Gas escapes during filling. Machines with tight seals prevent this. - Foaming
Foam increases waste. Adjusting speed reduces foam. - Equipment Wear
High pressure causes wear. Regular maintenance prevents breakdowns.
Benefits of Investing in a Quality Beverage Filling Machine
- Improved Efficiency
Machines save time. They fill bottles faster. - Better Quality Control
Automation ensures consistent results. - Lower Operational Costs
Machines use resources efficiently. - Eco-Friendly Options
Many models now include energy-saving features.
Maintenance Tips for High-Pressure Automatic Filling Machines
- Regular Cleaning
Clean the system after each use. This prevents contamination. - Inspect Valves
Check pressure valves regularly. Replace worn parts immediately. - Lubricate Parts
Keep moving parts lubricated. This reduces wear. - Software Updates
Update the machine’s software often. It improves performance.
High-pressure beverages need reliable equipment. A beverage filling machine offers precision and safety. An automatic filling machine ensures efficiency. Investing in these systems boosts production. It also improves product quality. Choose advanced machines for better results.