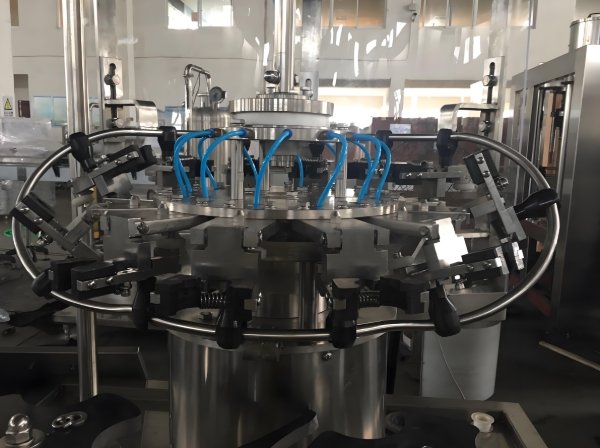
A Beverage Filling Machine streamlines production. But even the best machines face problems. Issues disrupt operations and reduce efficiency. Knowing these problems and solutions is essential.
An Automatic Filling Machine offers automation. It reduces human error. However, it still needs regular care. This article explains common problems and fixes.
Inconsistent Filling Levels
This issue is frequent. Containers may have uneven liquid levels. It happens due to misaligned nozzles or faulty sensors.
Fix:
- Check and realign the nozzles.
- Inspect sensors for defects. Replace if necessary.
- Clean nozzles to remove blockages.
An Automatic Filling Machine usually alerts operators to such problems. Use its diagnostics to identify issues.
Leakage During Filling
Leakage wastes liquid and slows production. It often results from damaged seals or worn-out valves.
Fix:
- Replace damaged seals immediately.
- Inspect valves for wear and tear. Replace if required.
- Tighten all connections to prevent leaks.
Regular maintenance of a Beverage Filling Machine prevents leaks.
Machine Jamming
Jamming occurs when bottles or caps misalign. It halts production and damages the machine.
Fix:
- Ensure proper alignment of containers.
- Use high-quality bottles and caps.
- Clean the conveyor belt regularly.
An Automatic Filling Machine includes sensors. These help detect jams early.
Slow Operation
Over time, a Beverage Filling Machine may slow down. This affects productivity. The issue often arises from dirt buildup or worn parts.
Fix:
- Clean the machine thoroughly.
- Lubricate moving parts to reduce friction.
- Replace worn components.
For an Automatic Filling Machine, update the software. This ensures optimal performance.
Overfilling or Underfilling
Incorrect filling amounts waste resources. Faulty sensors or calibration errors cause this.
Fix:
- Calibrate the machine according to manufacturer guidelines.
- Replace defective sensors.
- Monitor fill levels closely during operation.
An Automatic Filling Machine allows easy recalibration. Use its settings to make adjustments.
Electrical Failures
Electrical problems can stop a Beverage Filling Machine. These issues may include faulty wiring or power surges.
Fix:
- Inspect electrical components regularly.
- Replace damaged wires or fuses.
- Use surge protectors to safeguard circuits.
Consult a professional for major electrical repairs.
Spillage on Conveyor Belt
Spillage creates mess and delays. It also poses safety hazards. This happens due to improper nozzle operation or bottle misplacement.
Fix:
- Realign nozzles to minimize spillage.
- Adjust bottle holders for better positioning.
- Clean the conveyor belt after every shift.
Modern Automatic Filling Machines have spill-detection features. Enable these to minimize waste.
Uneven Bottle Sealing
Poor sealing compromises product quality. It occurs when caps don’t align correctly or sealing heads malfunction.
Fix:
- Check cap alignment on the conveyor.
- Test the sealing head for defects. Replace if needed.
- Adjust torque settings on the sealing unit.
An Automatic Filling Machine often includes automated capping. This reduces sealing errors.
Noise During Operation
Unusual noise indicates internal issues. It could result from loose parts or lack of lubrication.
Fix:
- Tighten any loose bolts or screws.
- Apply lubricant to moving parts.
- Inspect for damaged gears or belts. Replace them.
A well-maintained Beverage Filling Machine operates quietly.
Sensor Malfunction
Sensors control many functions. A faulty sensor disrupts the entire process.
Fix:
- Test sensors regularly for accuracy.
- Replace malfunctioning sensors.
- Ensure proper wiring and connections.
An Automatic Filling Machine alerts users to sensor issues. This simplifies troubleshooting.
Preventive Maintenance Tips
Preventing issues is better than fixing them. Follow these tips:
- Clean the Beverage Filling Machine daily.
- Lubricate parts as per the manual.
- Check and replace worn components.
- Update software in Automatic Filling Machines.
- Train operators on machine handling.
Regular maintenance extends machine life.
Benefits of Timely Repairs
Addressing problems quickly has benefits. These include:
- Reduced downtime.
- Lower repair costs.
- Consistent product quality.
- Enhanced machine efficiency.
Timely repairs keep the Beverage Filling Machine running smoothly.
A Beverage Filling Machine is essential for production. But it faces challenges. Knowing common problems and fixes ensures smooth operations.
An Automatic Filling Machine offers advanced features. Use them wisely to avoid disruptions. Regular maintenance and quick repairs maximize productivity.
Invest time in care, and the machine will serve you well. For high-volume production, a reliable machine is a must. Choose wisely and maintain it properly.