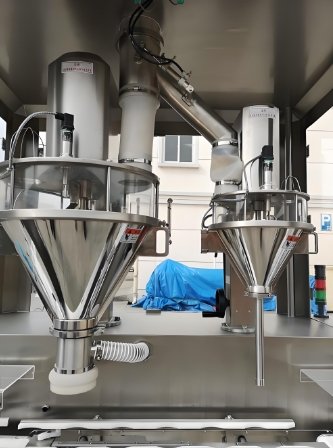
The speed of a Powder Filling Machine impacts production efficiency and product quality. Finding the right balance between speed and accuracy is essential for achieving optimal results. Whether using a semi-automatic or an Automatic Filling Machine, understanding filling speed is crucial for smooth operations.
This article explores the factors influencing filling speed, how to choose the right settings, and the role of automation in optimizing performance.
Why Filling Speed Matters
Filling speed directly affects productivity and precision.
Benefits of the Right Speed:
- Higher Efficiency: Meet production targets on time.
- Improved Accuracy: Prevent overfilling or underfilling.
- Reduced Waste: Avoid spillage or material loss.
- Consistent Quality: Ensure uniform product packaging.
Incorrect speed settings can cause errors and slow down operations.
Factors That Influence Filling Speed
Several factors determine the optimal speed of a Powder Filling Machine:
1. Powder Characteristics
- Free-flowing powders fill faster.
- Sticky or clumpy powders require slower speeds.
2. Machine Type
- Semi-automatic machines need manual intervention, which affects speed.
- Automatic Filling Machines operate continuously and handle high speeds efficiently.
3. Container Size
- Small containers fill quicker.
- Larger containers may need precise adjustments to prevent overflow.
4. Production Volume
- High-volume production requires faster speeds.
- Smaller batches allow for slower, more precise filling.
5. Environmental Factors
- Humidity and temperature can affect powder flow.
- Stable conditions help maintain consistent speed.
Types of Filling Speeds in Powder Filling Machines
1. Low-Speed Filling
- Best for sensitive powders or small-scale production.
- Ensures accuracy with minimal waste.
2. Medium-Speed Filling
- Balances speed and precision.
- Ideal for moderate production volumes.
3. High-Speed Filling
- Suitable for large-scale operations.
- Works well with free-flowing powders and uniform containers.
Automatic Filling Machines excel at high-speed operations without compromising accuracy.
How to Choose the Right Filling Speed
1. Assess Production Needs
Evaluate your daily production targets.
- Choose higher speeds for large orders.
- Opt for slower speeds if accuracy is a priority.
2. Match Speed to Powder Type
Adjust the speed based on powder flowability.
- Sticky powders need slower speeds to prevent clogging.
- Free-flowing powders can handle faster speeds.
3. Consider Container Specifications
- Use slower speeds for irregular or delicate containers.
- Faster speeds are ideal for uniform containers.
4. Test and Adjust Settings
Conduct trial runs with your Powder Filling Machine.
- Fine-tune settings for optimal results.
- Monitor accuracy and efficiency during tests.
The Role of Automatic Filling Machines
An Automatic Filling Machine simplifies speed adjustments.
Advantages of Automatic Machines:
- Real-Time Monitoring: Sensors adjust speed based on powder flow.
- Pre-Set Programs: Choose from speed presets for different products.
- High Output: Maintain consistent performance at faster speeds.
Automation ensures precision even at high speeds, making it ideal for large-scale operations.
Challenges in Adjusting Filling Speed
1. Inconsistent Filling
Cause: Improper speed settings.
Solution: Calibrate the machine regularly.
2. Powder Spillage
Cause: Speed too high for container size.
Solution: Reduce speed to match container capacity.
3. Machine Wear and Tear
Cause: Prolonged high-speed operations.
Solution: Schedule regular maintenance.
4. Clogging
Cause: Sticky powders at high speeds.
Solution: Slow down and clean components regularly.
Maintenance Tips for Speed Optimization
Proper maintenance keeps your Powder Filling Machine running efficiently.
1. Clean Regularly
- Remove powder residues from hoppers and nozzles.
- Prevents blockages that slow down operations.
2. Inspect Components
- Check for wear on auger screws and nozzles.
- Replace damaged parts promptly.
3. Calibrate Frequently
- Ensure speed settings align with production needs.
- Maintain accuracy and consistency.
4. Lubricate Moving Parts
- Reduce friction for smoother operations.
- Extend the machine’s lifespan.
Benefits of Optimizing Filling Speed
1. Enhanced Productivity
The right speed increases output without sacrificing quality.
2. Reduced Costs
Minimize waste and avoid unnecessary downtime.
3. Improved Accuracy
Maintain consistent product weight and appearance.
4. Flexibility
Adjust speeds to accommodate various powders and containers.
Real-World Applications of Speed Adjustment
1. Pharmaceutical Industry
- Slower speeds for accurate medicine doses.
- Faster speeds for bulk production of supplements.
2. Food Industry
- Adjust speed for powders like spices, protein mixes, and baking ingredients.
3. Cosmetics Industry
- Slower speeds ensure precise filling of compact powders and makeup.
4. Chemical Industry
- Use high speeds for large volumes of fertilizers or detergents.
The Future of Speed Optimization
Modern Powder Filling Machines use advanced technology to improve speed control.
Innovations:
- IoT Integration: Real-time speed adjustments based on production data.
- AI Algorithms: Predict and prevent filling errors.
- Smart Sensors: Automatically adapt to powder characteristics.
These advancements make speed adjustments seamless and efficient.
Choosing the right filling speed for your Powder Filling Machine is essential for efficient production and quality results. Assess your powder type, container size, and production volume to determine the optimal speed. For high-speed operations with precision, an Automatic Filling Machine is the best solution.
Regular maintenance and modern features ensure consistent performance at any speed. Invest in the right machine and settings to maximize productivity while maintaining quality.