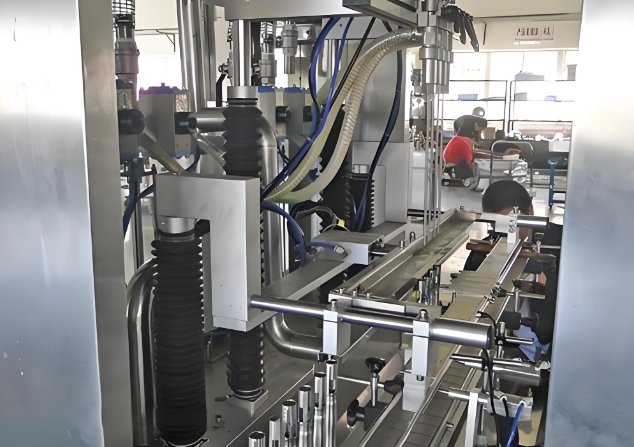
Energy efficiency is a top priority in manufacturing. For companies using filling machines and automatic filling machines, cutting energy costs without compromising performance is crucial. By following a few best practices, manufacturers can save energy, lower operating costs, and boost sustainability.
1. Regular Maintenance for Optimal Efficiency
Maintenance is essential. Routine checks keep a filling machine in top shape. Maintenance reduces friction, leaks, and malfunctions. An automatic filling machine needs regular lubrication, cleaning, and inspection. This helps reduce energy consumption and improves efficiency.
2. Monitor and Control Temperature
Heat management saves energy. Automatic filling machines generate heat during operation. Managing this temperature reduces the energy needed to keep machines cool. Using efficient ventilation or temperature controls helps stabilize machine temperatures, saving energy.
3. Invest in Energy-Efficient Components
Choose energy-efficient components. High-quality motors, sensors, and pumps for filling machines can make a difference. They reduce energy waste and work effectively with less power. Investing in these parts for an automatic filling machine leads to long-term energy savings.
4. Implement Variable Speed Drives (VSDs)
Variable Speed Drives (VSDs) adjust motor speeds based on the process needs. This feature saves energy in filling machines that do not always need to operate at full speed. For an automatic filling machine, VSDs can adjust filling speeds according to product flow, reducing energy use during slower cycles.
5. Insulate and Seal to Prevent Losses
Prevent energy loss with insulation and sealing. Many filling machines lose energy through air or liquid leaks. Insulating pipes and sealing gaps prevents heat and fluid loss. This keeps an automatic filling machine more efficient and minimizes wasted energy.
6. Optimize Air Compression Systems
Compressed air systems are energy-intensive. Many filling machines use air pressure for operations. Optimizing air systems reduces energy demand. Regularly inspect air compressors for leaks and consider using energy-saving modes when the automatic filling machine is idle.
7. Use Smart Technology for Real-Time Monitoring
Smart sensors track energy use in real-time. Sensors installed on filling machines provide valuable data on energy consumption. Automatic filling machines equipped with smart tech can detect inefficiencies instantly, allowing adjustments before energy waste occurs.
8. Minimize Idle Time
Idle time wastes energy. When not in use, filling machines continue to consume power. Reducing idle times by scheduling machine breaks can save energy. Many automatic filling machines now have standby or sleep modes to cut energy use during inactivity.
9. Install Energy-Efficient Lighting
Well-lit workspaces improve productivity and safety. Using LED or other energy-efficient lights near filling machines reduces electricity costs. Ensuring proper lighting around an automatic filling machine also supports accurate filling, which minimizes waste.
10. Adjust Settings for Product Specifics
Match machine settings to the product. Every product has specific filling requirements. Adjusting speed, pressure, and volume on an automatic filling machine saves energy. For lighter or smaller products, lower speed and pressure reduce energy consumption.
11. Opt for Renewable Energy Sources
Switch to renewable power sources. Solar, wind, or hydroelectric energy helps reduce the carbon footprint of filling machines. Using renewable energy for an automatic filling machine makes operations more sustainable, lowering overall environmental impact.
12. Conduct Energy Audits
Audits identify areas for improvement. Regular energy audits on filling machines reveal waste and inefficiencies. After an audit, adjusting the automatic filling machine based on findings saves power and improves overall performance.
13. Implement a Preventive Maintenance Program
Preventive maintenance prevents unexpected issues. Checking components in filling machines before problems arise saves energy. A well-maintained automatic filling machine operates smoothly, without sudden breakdowns that cause energy spikes.
14. Use Inverter Technology
Inverters improve motor efficiency. Many automatic filling machines can benefit from inverter technology, which adjusts motor speeds as needed. Inverters reduce the strain on motors, conserving energy and extending the machine’s lifespan.
15. Integrate Energy Management Systems (EMS)
Energy Management Systems (EMS) track energy use across machines. EMS helps monitor filling machines and detect any spikes in consumption. The data from EMS allows adjustments to an automatic filling machine to maximize efficiency.
16. Optimize Filling Speeds for Efficiency
Slow speeds often waste energy. Optimizing the speed of filling machines for each product type helps reduce energy usage. For an automatic filling machine, matching speed to product density and viscosity can minimize the power required for each fill.
17. Reduce Water Usage in Cooling Systems
Cooling systems use a lot of water and energy. Using closed-loop cooling systems or air-cooled systems on filling machines conserves both water and energy. Efficient cooling supports the long-term efficiency of automatic filling machines.
18. Train Operators on Energy-Saving Techniques
Operators influence machine efficiency. Training them on energy-saving techniques helps minimize waste. Teaching operators how to handle automatic filling machines efficiently, adjust settings, and perform basic maintenance reduces energy consumption.
19. Schedule Operations During Off-Peak Hours
Energy costs vary by time of day. Running filling machines during off-peak hours lowers energy expenses. For companies using automatic filling machines, scheduling non-urgent production at night or weekends can result in significant savings.
20. Set Energy Goals and Track Progress
Tracking energy use helps achieve goals. Set measurable energy-saving targets for filling machines and monitor performance regularly. Tracking helps ensure that each automatic filling machine is operating at peak efficiency and meeting sustainability objectives.
Energy efficiency in filling machines is a growing priority for manufacturers. By following these best practices, companies can cut energy costs, reduce environmental impact, and maintain high productivity. Investing in these strategies for automatic filling machines helps create a more sustainable and cost-effective production process.